Aircraft Heat Sink
Aircraft C/C (Carbon Carbon) Heat Pack
We supply C/C heat packs for A320, A321, A330, A340, B737, B747, B777, E-145, F-100 etc.
Which heat packs do we supply?
Aircraft C/C (Carbon Carbon) Heat Packs
The CMC company supplies the aircraft carbon brakes to civil aviation market. Carbon brakes are widely installed on civil aircrafts. The main applications we have for airplanes are MA-60, A318, A319, A320, A330, Boeing 737, Boeing 757 etc. Carbon carbon heat packs offer a significant weight savings compared to traditional steel brakes or powder metallurgy brakes. And weight savings can reduce the fuel consumption for airplanes. Also, the carbon carbon aircraft brakes have twice longer life than steel brakes. We can also re-condition the carbon brakes after their first life cycle end. After re-conditioned, we can use them again. What’s more, carbon brakes have can absorb huge enerygy during landing braking. And we have developed the lastest anti-oxidation coating technology. The carbon brake discs will be protected well from oxidized when turning red. Thus the carbon brakes will have longer life-span.
Certification and Qualification of our Products
The PMA parts we are supplying are CAAC certified. And, we can produce any shapes of carbon brakes according to customer’s drawings. The following applications are the main aircrafts we are supllying to. We are supplying our aircraft brakes to different countries, including Chinese mainland, middle-East, South Aisa, Central Aisa, Africa ect. Not only the carbon brakes, we also supply steel brakes and power metallurgy brakes to global customers.
- Airworthiness certification for MA60 (already supplied several thousand pairs of carbon carbon brakes)
- B737 series powder metallurgy brakes with PMA Certification
- B737 & A320 series carbon carbon brakes with PMA Certification
- A330 series carbon carbon brakes with PMA Certification
- Supplying to China Eastern Airlines
Please email us for more information and full list. Also, we have huge inventory of FAA/EASA certified landing gear components to supply.
For automotive carbon carbon brakes and carbon ceramic brakes, please go to this page.
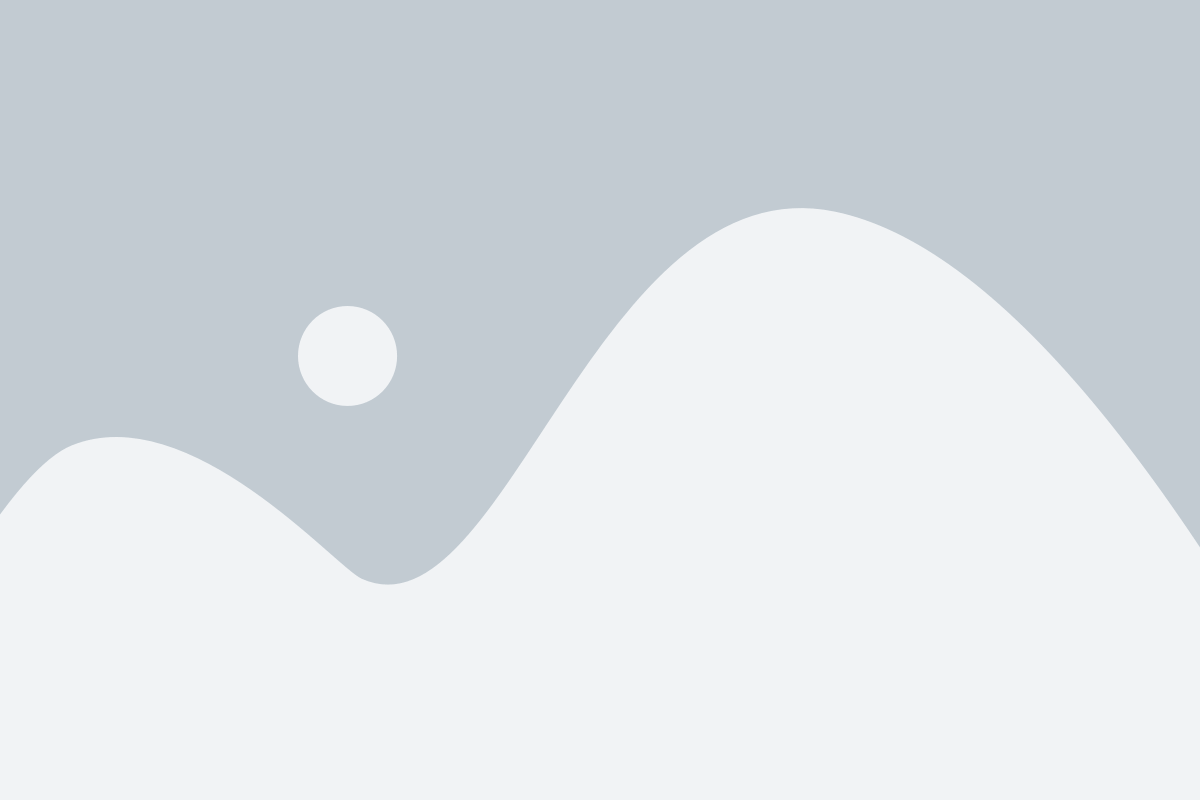
A321 Heat Packs
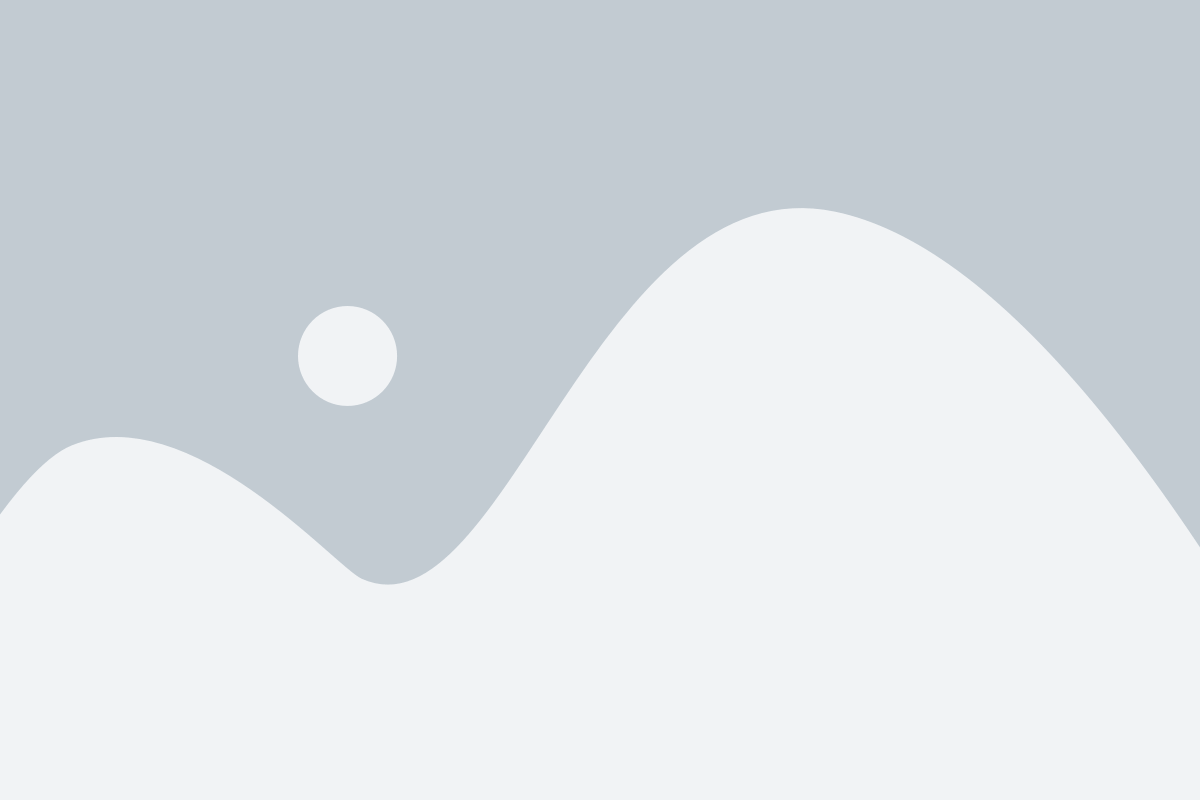
A330-200/300, A340-200/300 Heat Packs
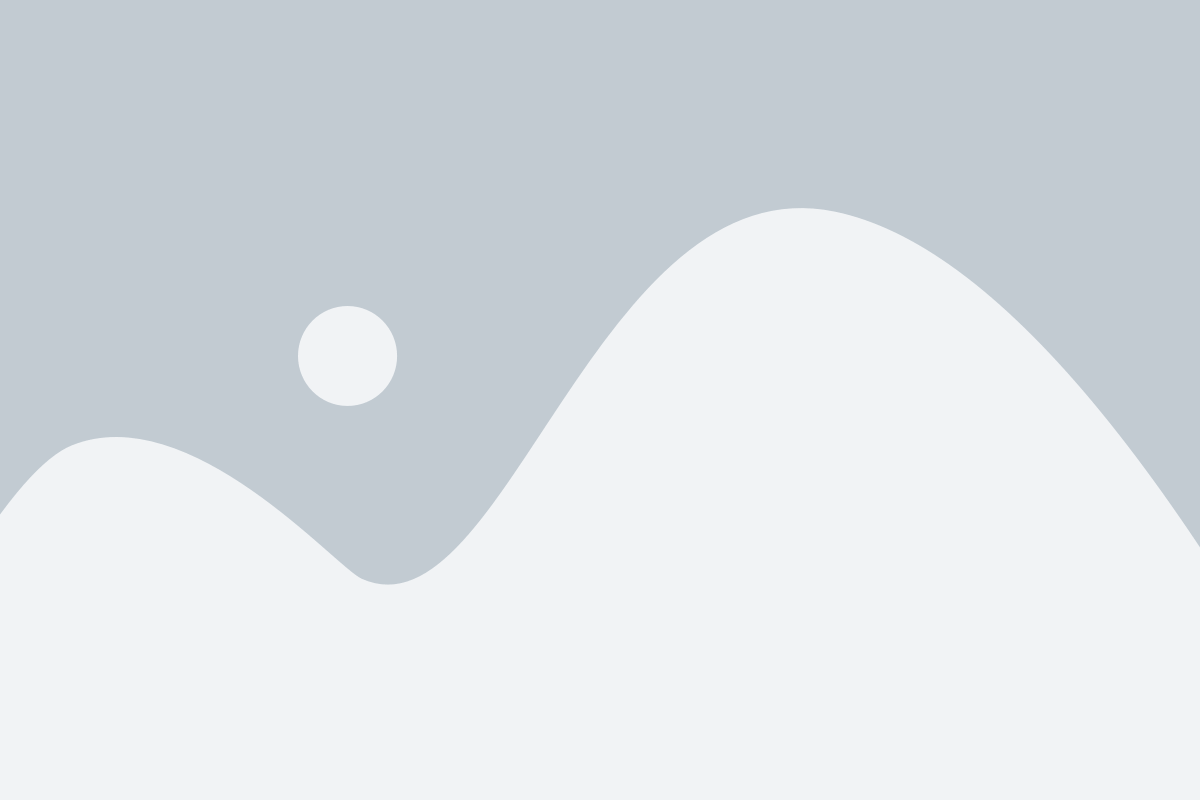
A340-500/600 Heat Packs
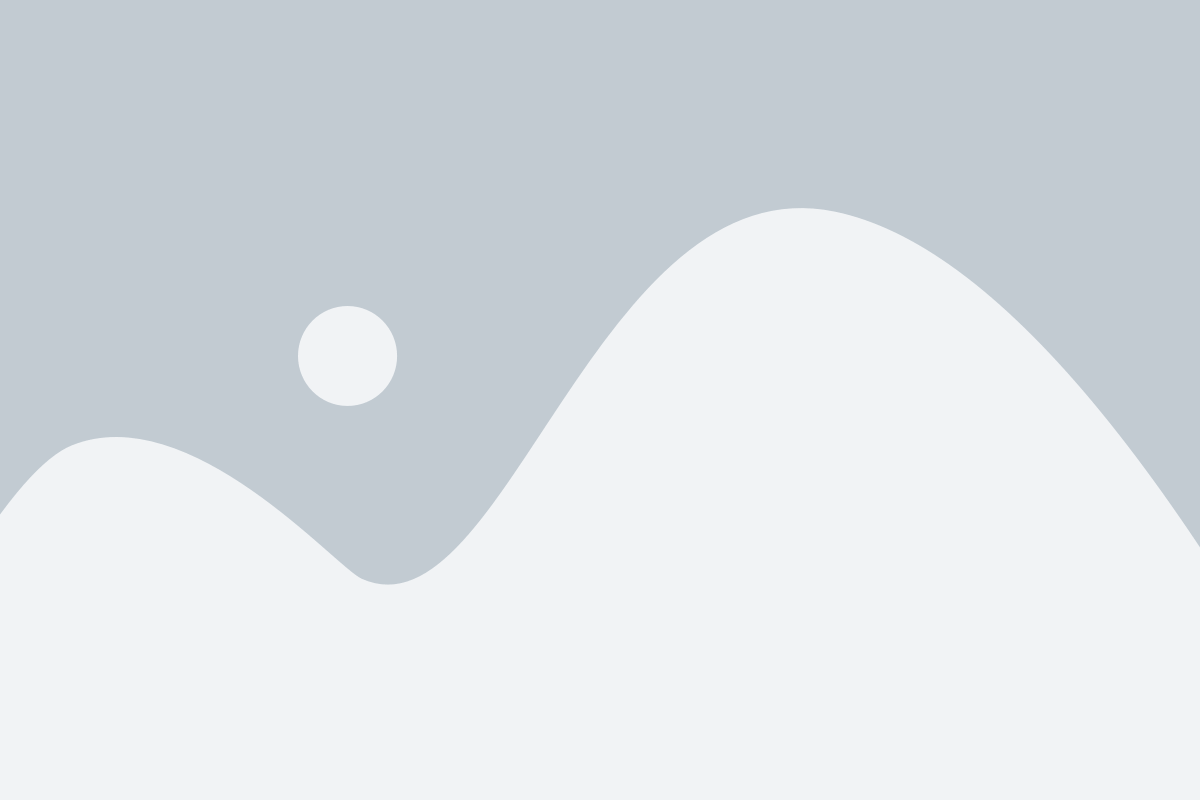
B737-800/900/BBJ, B737-8 Heat Packs
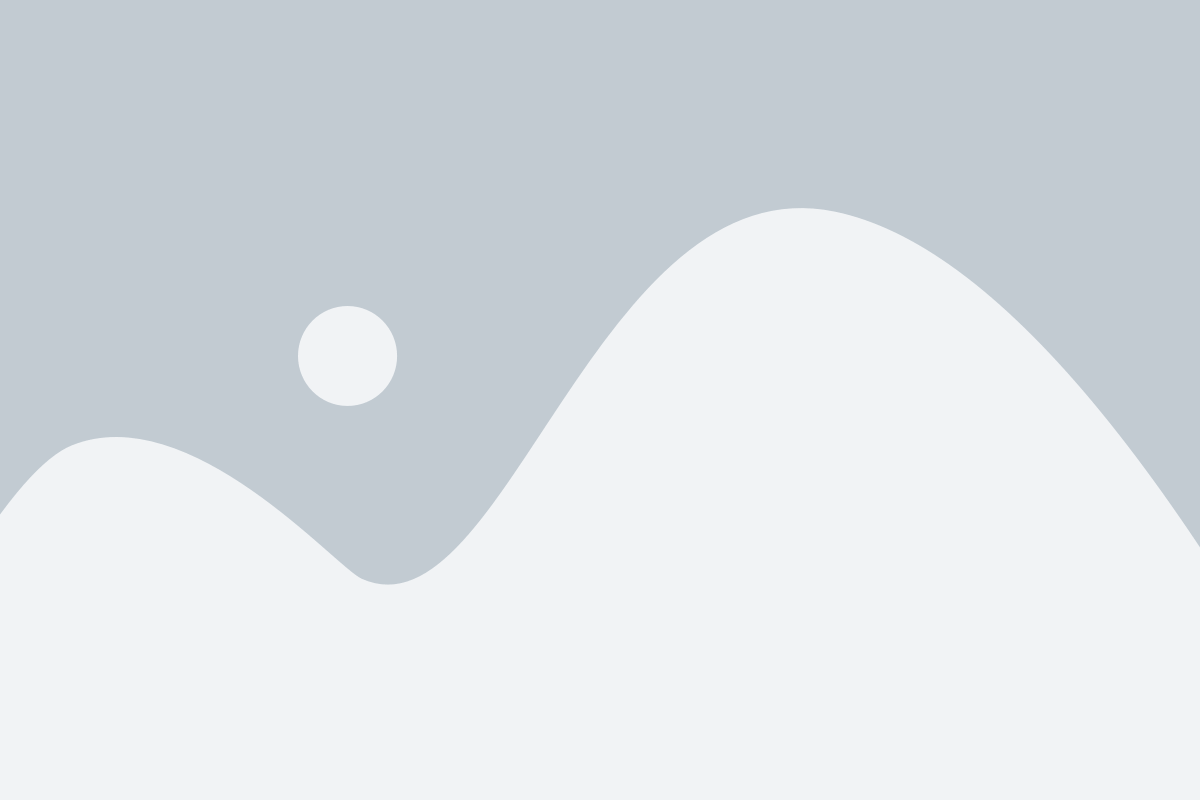
B747-400/400F Heat Packs
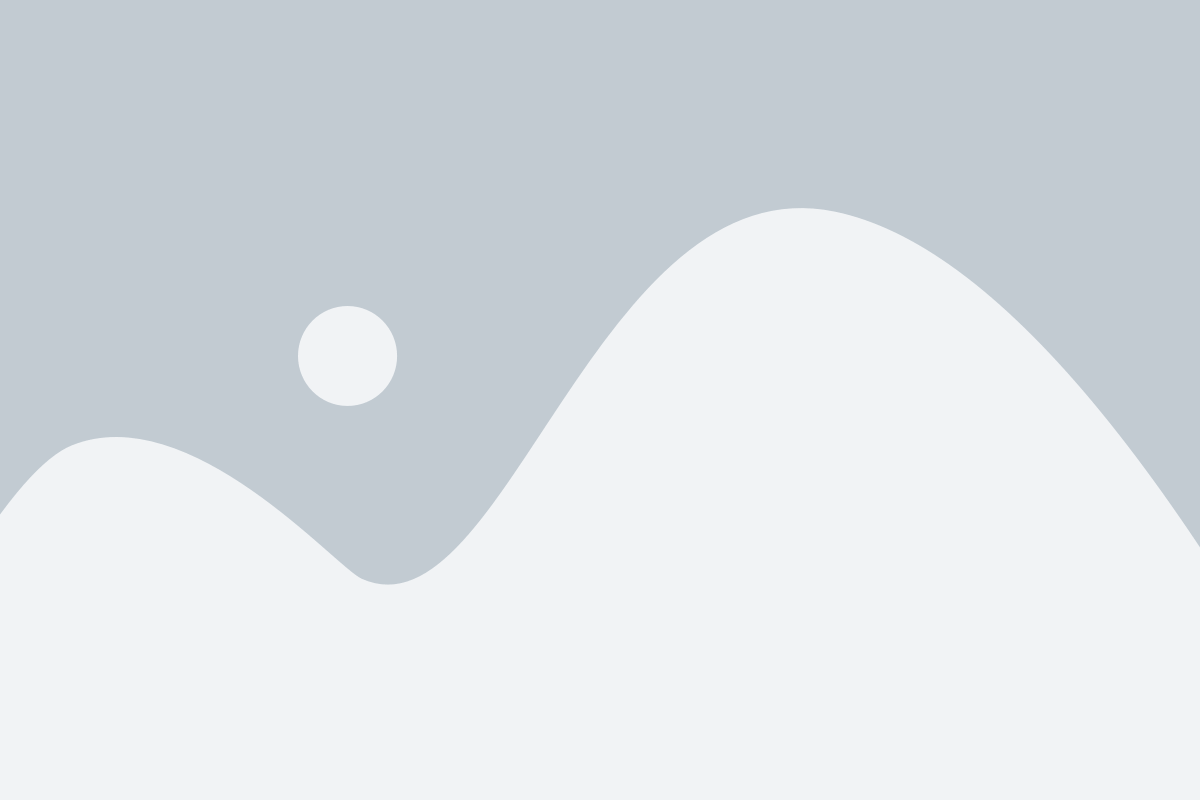
B757-200 Heat Packs
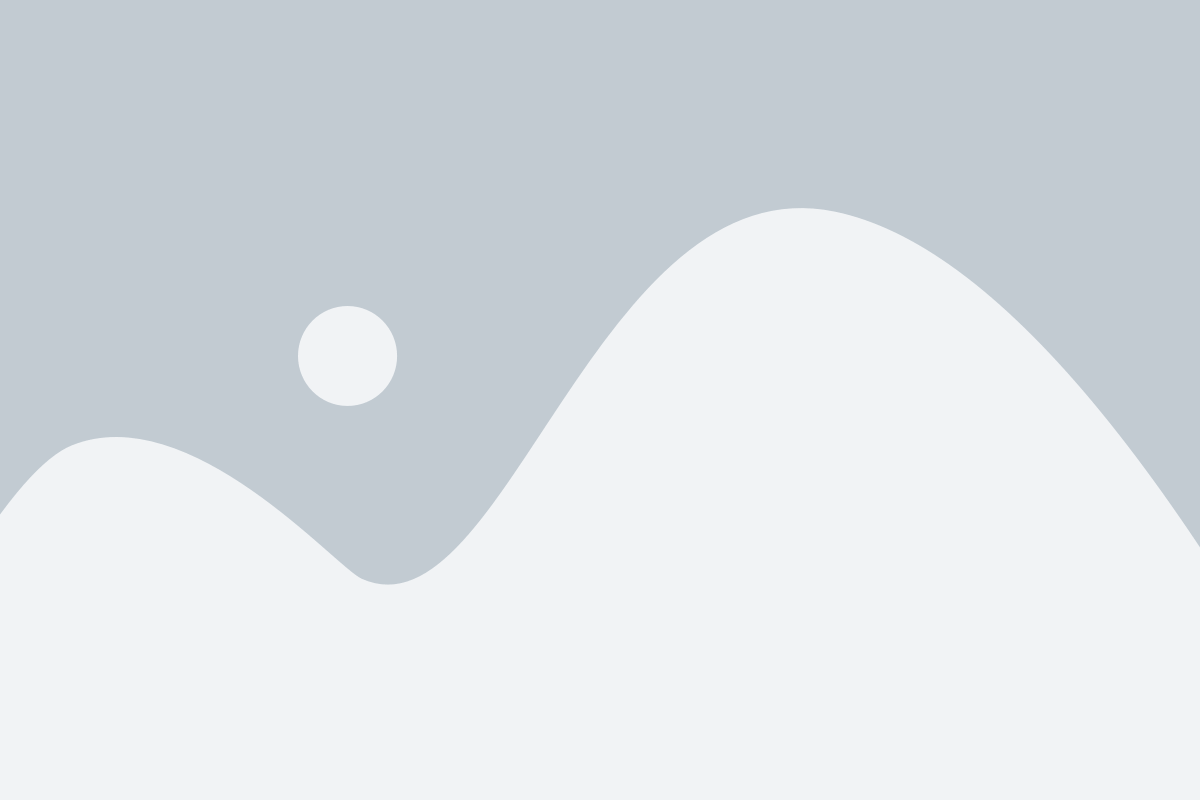
B767-300 Heat Packs
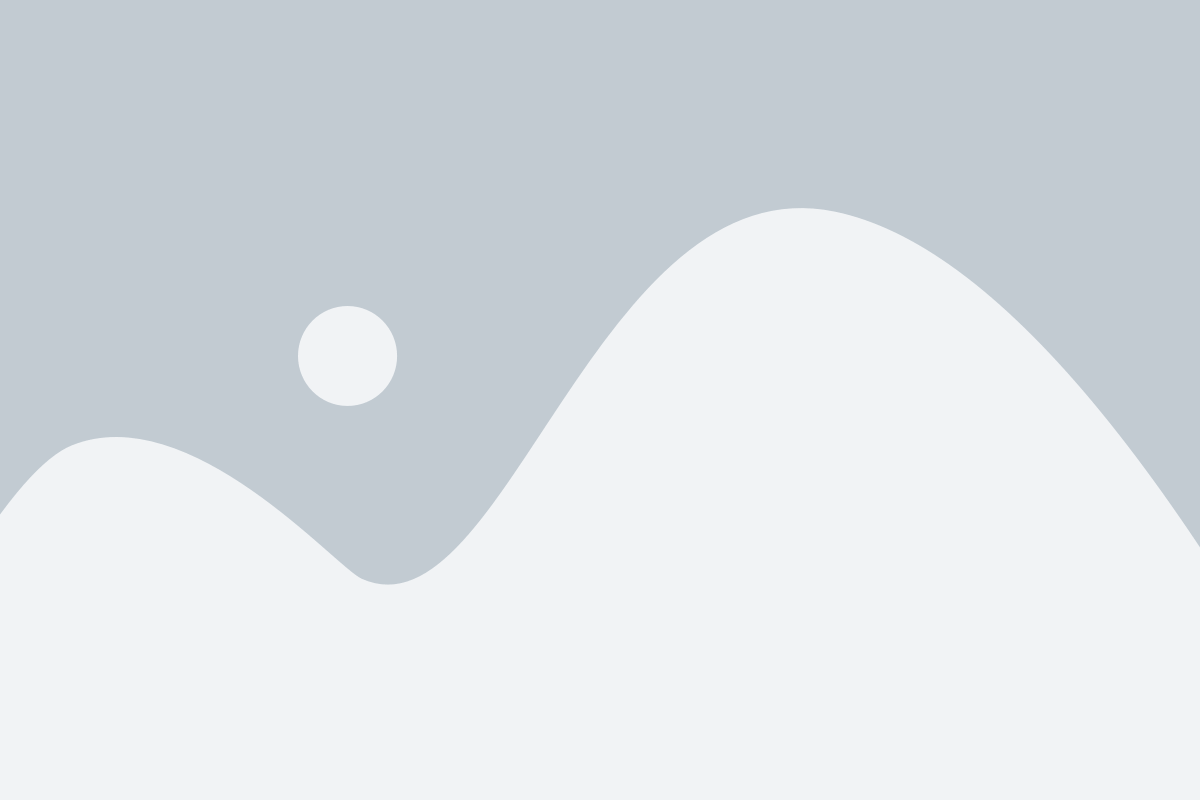
B777 Heat Packs
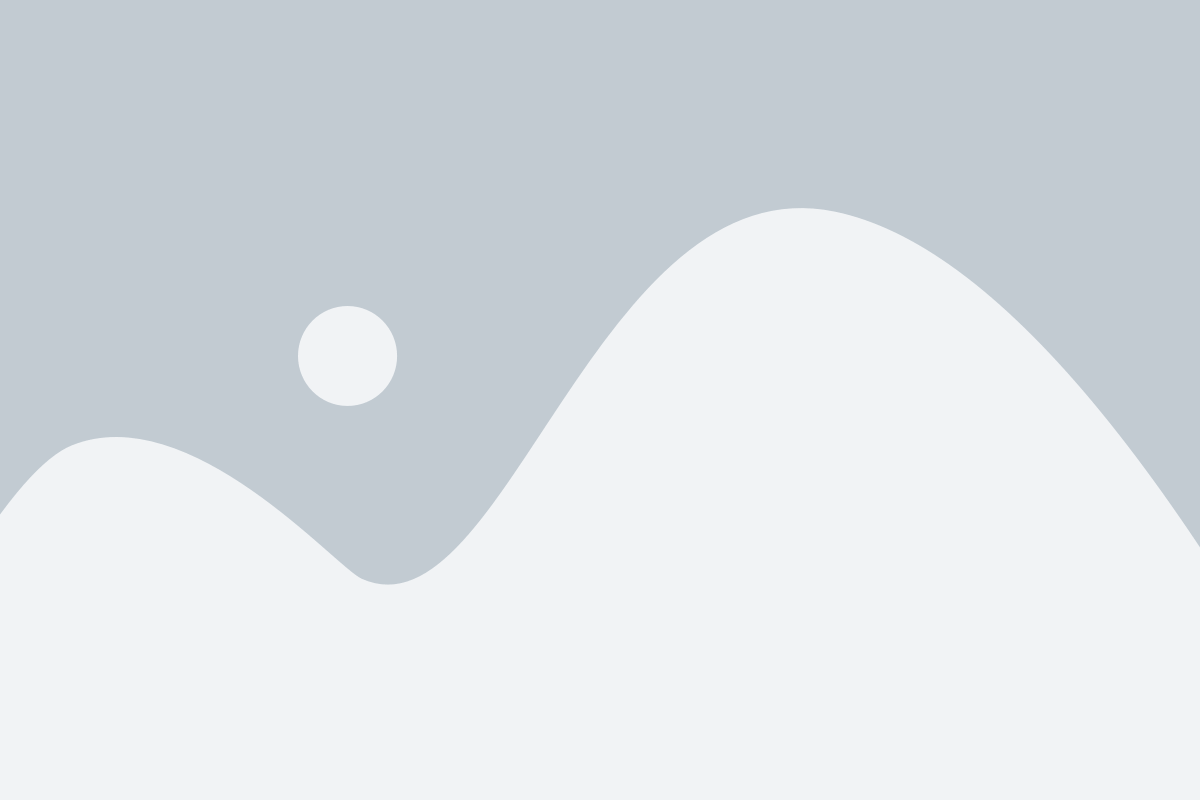
BAe146 Heat Packs
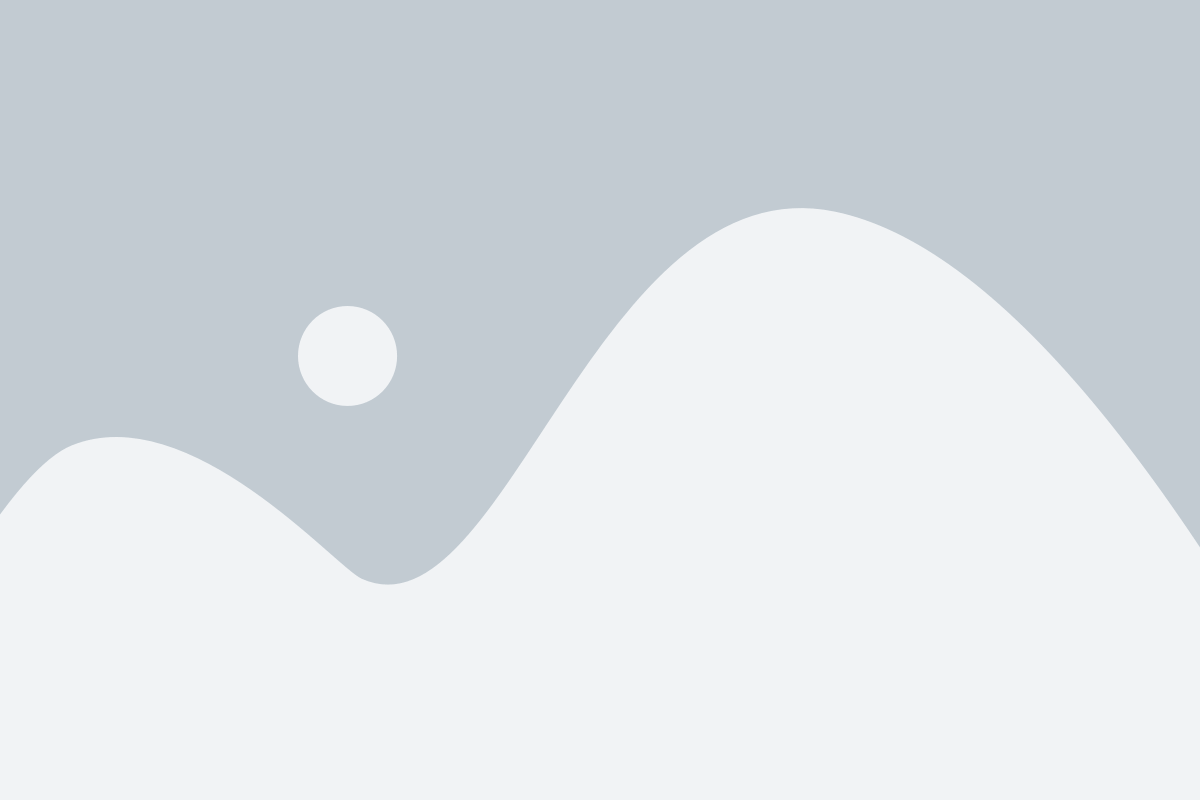
ERJ-135/140/145 Heat Packs
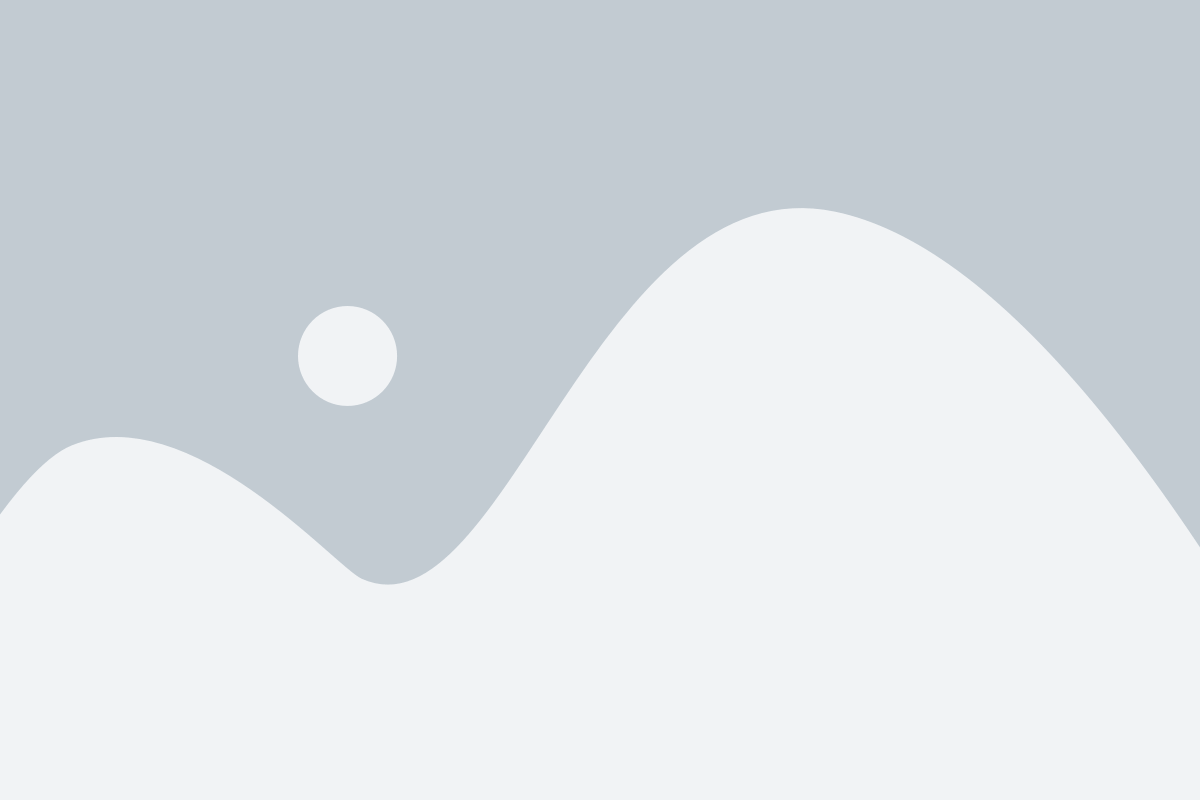
ERJ-190/195 Heat Packs
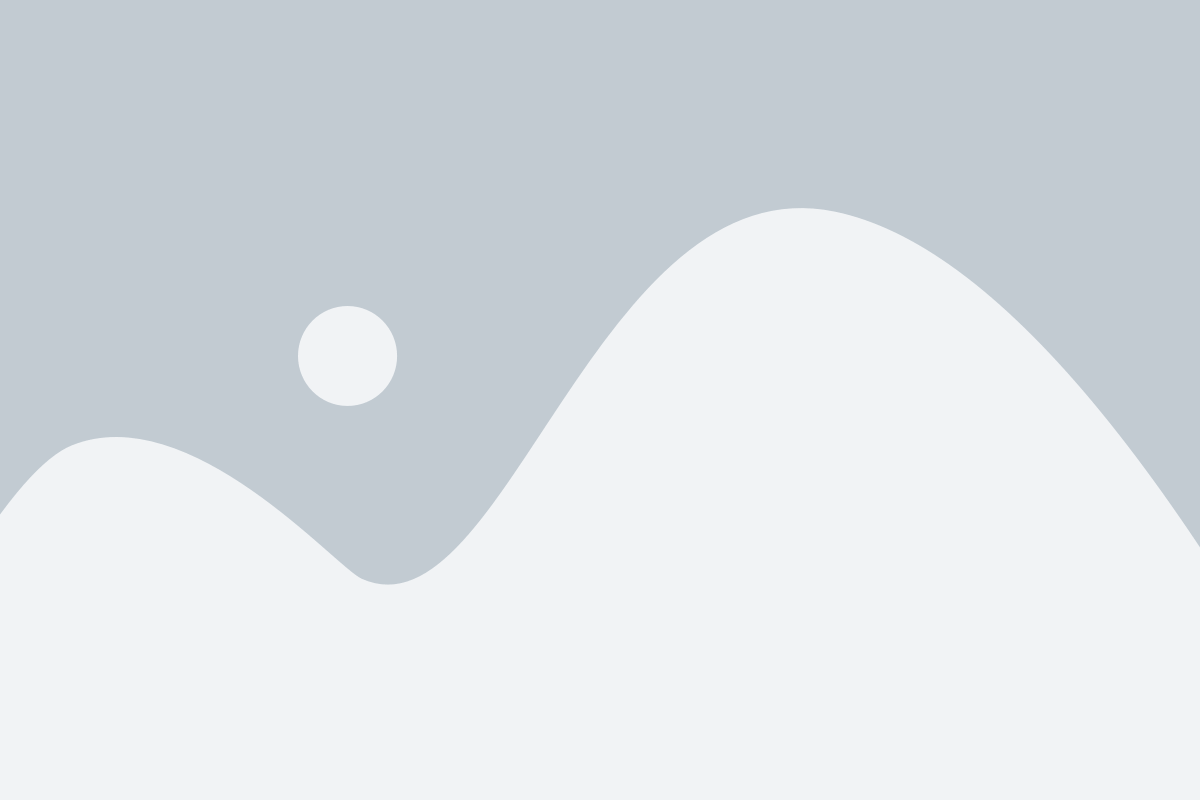
Fokker 100 Heat Packs
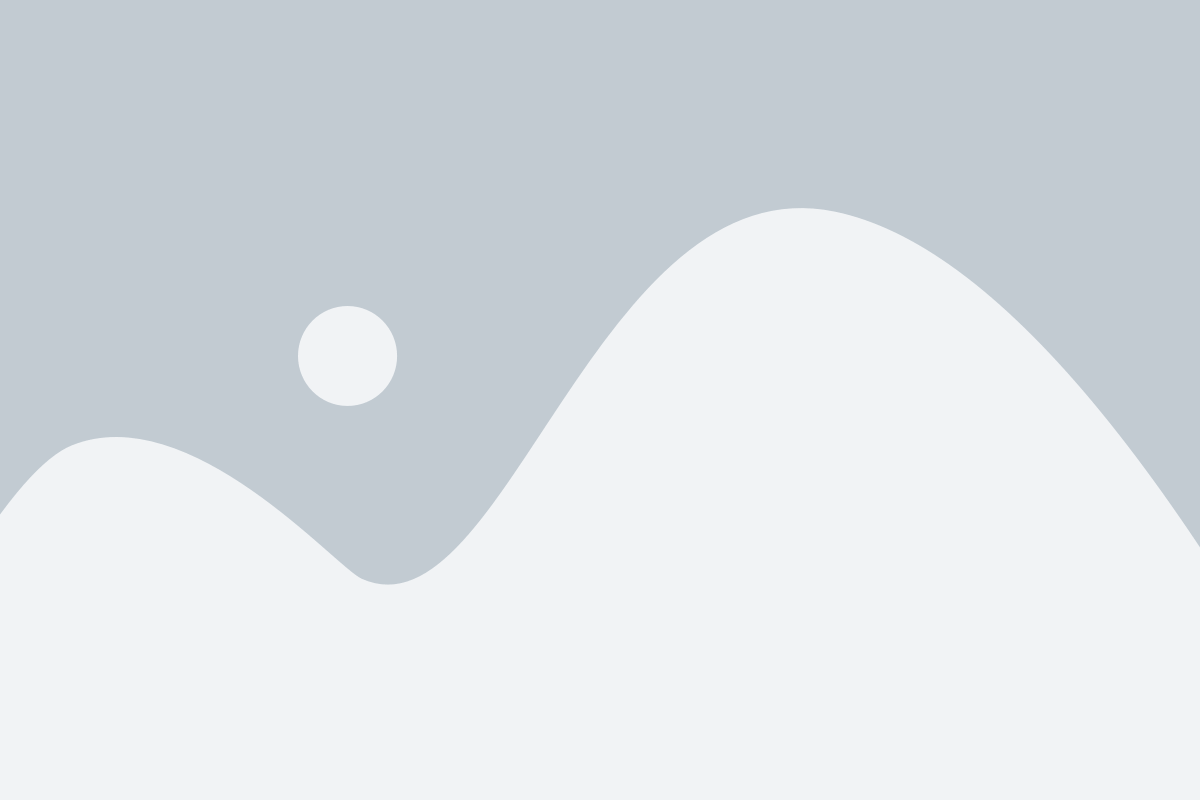
MA-60 Heat Packs
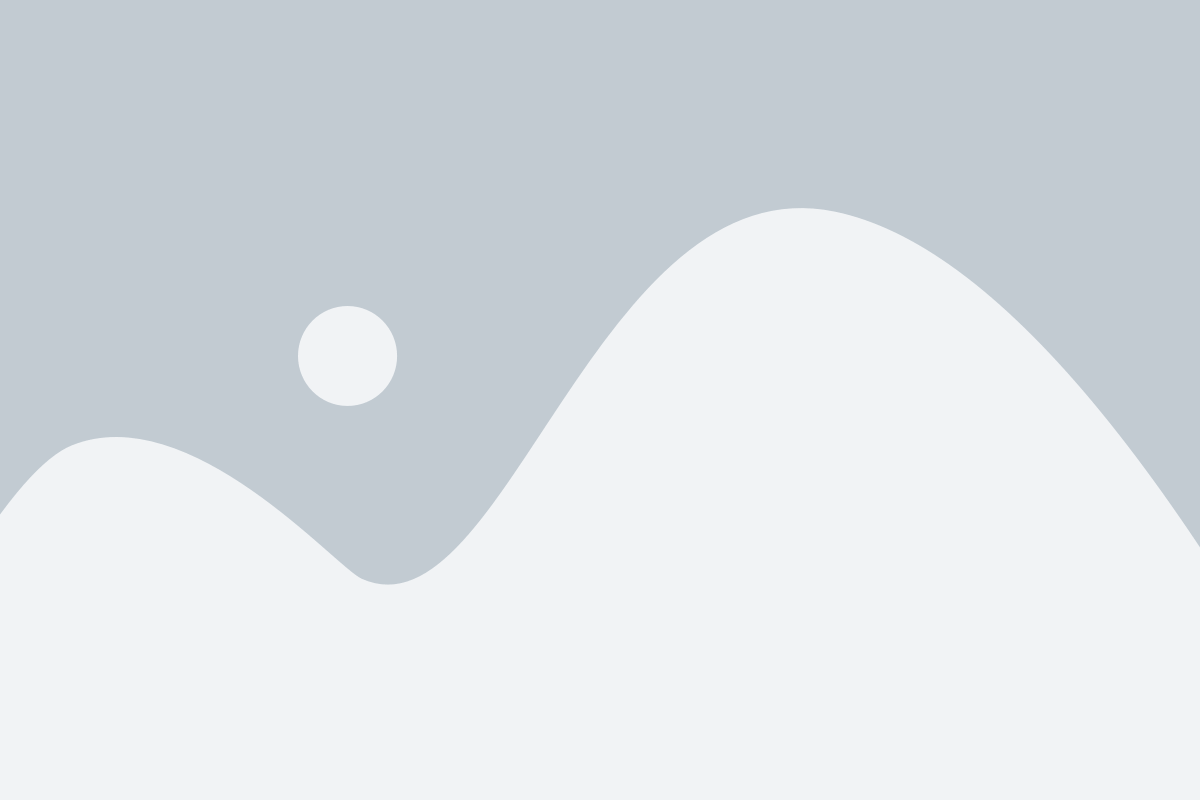
ARJ21 Heat Packs
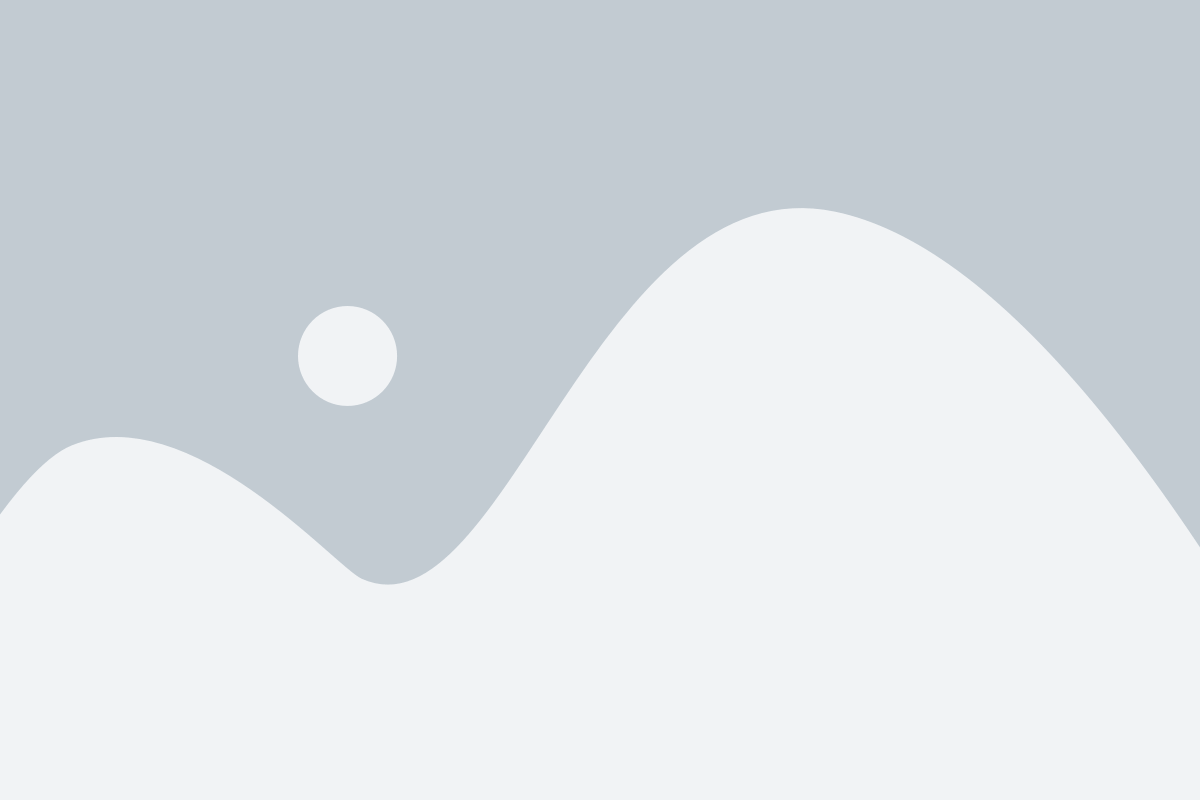
ERJ-135/140/145 Heat Packs
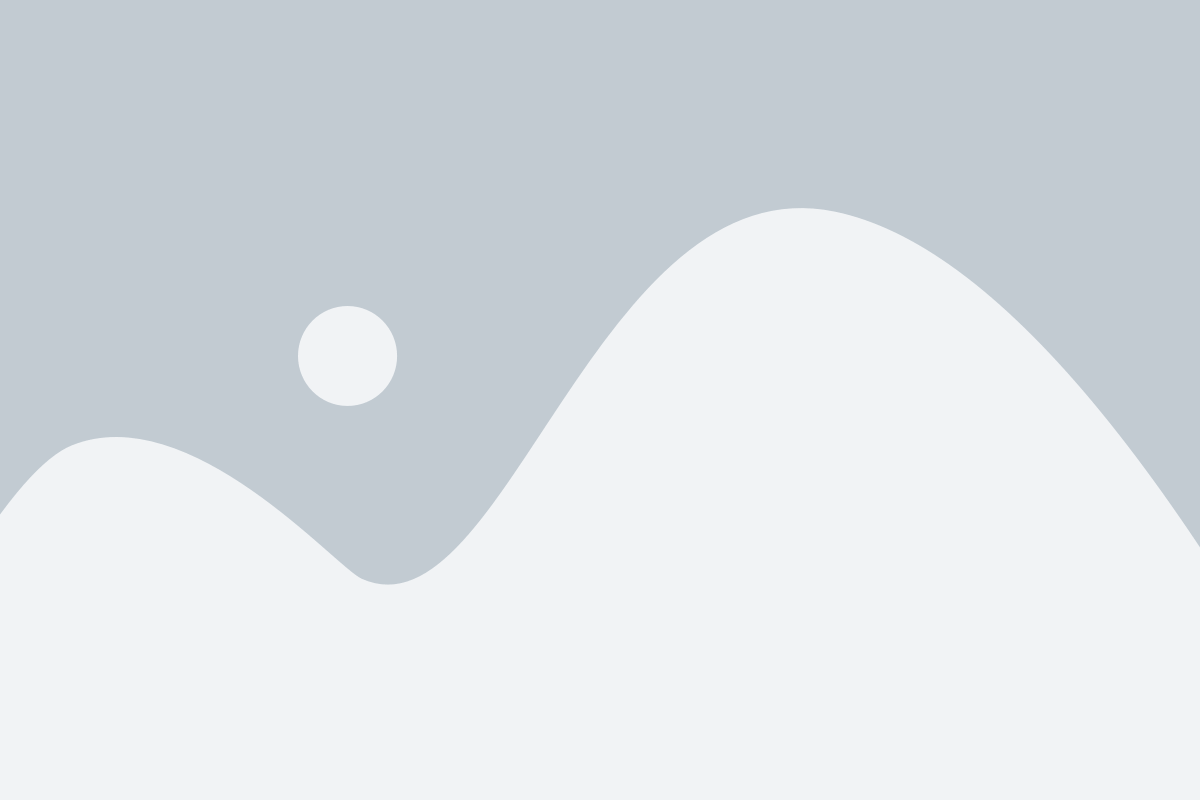
ERJ-135/140/145 Heat Packs
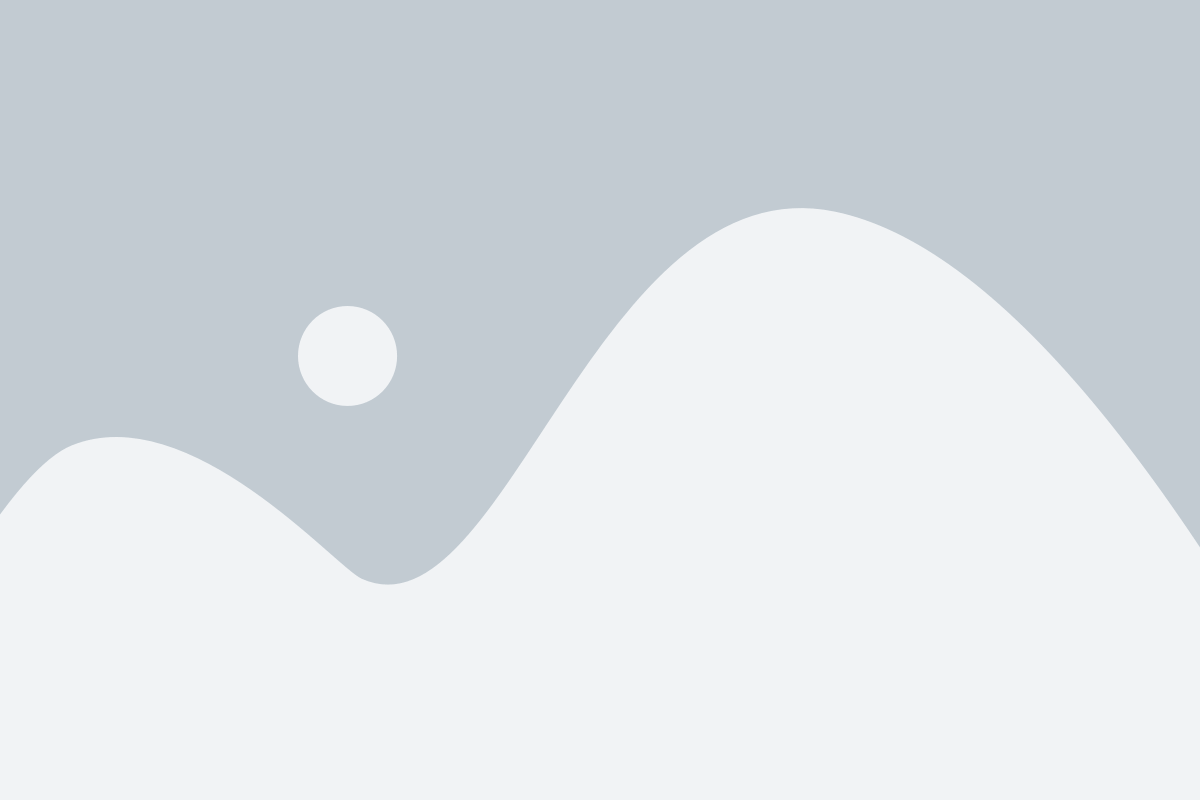
More Heat Packs
FAQ On Aircraft Brake Carbon Carbon Heat Packs
Table of Contents
Charpter 1
What are the specific properties of carbon-carbon composites that make them ideal for aircraft brake systems?
Carbon-carbon (C/C) composites are highly valued in aircraft brake systems due to their unique properties that are well-suited to the demanding requirements of aviation braking. Here are some of the specific properties that make C/C composites ideal for this application:
High-Temperature Resistance:
- Endurance: C/C composites can withstand extremely high temperatures (up to 2,500 degrees Celsius) without losing structural integrity or performance.
- Stability: They maintain mechanical stability even under these extreme conditions, which is crucial during the intense heat generation of aircraft landings.
Low Thermal Expansion:
- Dimensional Stability: These materials exhibit very low thermal expansion, which ensures dimensional stability under varying thermal conditions. This characteristic is critical for maintaining precise clearances between the brake disc and pad, ensuring consistent braking performance.
High Thermal Conductivity:
- Heat Dissipation: C/C composites efficiently conduct heat away from the brake surface, reducing the risk of overheating and brake fade during repeated or prolonged braking scenarios typical in aviation.
High Specific Strength and Stiffness:
- Performance Under Load: The strength-to-weight ratio of C/C composites is exceptionally high, which is vital for maintaining brake performance under the high mechanical loads experienced during aircraft operations.
- Reduced Weight: This also contributes to overall weight savings in the aircraft, which is a critical factor in aerospace design for fuel efficiency and payload maximization.
Wear Resistance:
- Durability: Carbon-carbon composites show excellent resistance to wear even under harsh operating conditions. This wear resistance translates into longer life spans for brake components, reducing the need for frequent replacements.
Frictional Properties:
- Consistent Friction Coefficient: They maintain a consistent coefficient of friction over a wide range of temperatures and operational conditions, providing reliable braking performance.
Fatigue Resistance:
- Cyclic Loading: C/C composites withstand the cyclic loading and unloading of stresses without significant fatigue, which is crucial for the safety and reliability of aircraft braking systems.
Corrosion Resistance:
- Chemical Stability: Unlike metals, C/C composites are inert and resistant to corrosion from environmental exposure and chemicals, including hydraulic fluids and deicing salts.
These properties make carbon-carbon composites an excellent material choice for aircraft brake systems, particularly in military, commercial, and high-performance aircraft, where reliability, efficiency, and performance are critical. The combination of high-temperature capabilities, strength, and longevity under demanding conditions are why C/C composites are preferred over other materials like steel or aluminum in advanced braking systems.
Charpter 2
How do the thermal properties of C/C composites compare to other materials like steel or ceramic in aviation brake systems?
The thermal properties of carbon-carbon (C/C) composites make them highly suitable for aviation brake systems, especially when compared to other common materials like steel or ceramic. Here’s a comparative analysis of these materials based on their thermal characteristics:
Carbon-Carbon (C/C) Composites
High-Temperature Resistance:
- C/C composites can withstand temperatures up to 2,500 degrees Celsius without degradation, which is significantly higher than what steel or ceramic can handle.
Thermal Conductivity:
- C/C composites have good thermal conductivity, allowing for efficient heat dissipation. This characteristic helps in managing the heat generated during braking and reduces the risk of brake fade.
Low Thermal Expansion:
- They exhibit very low thermal expansion, which ensures that the structural integrity and dimensional stability are maintained even under high thermal loads. This is crucial for maintaining the performance and reliability of brake systems.
Steel (Typically Used in Standard Aviation Brakes)
High-Temperature Resistance:
- Steel can withstand high temperatures but is prone to losing some mechanical properties such as strength and hardness at temperatures above 500 degrees Celsius.
Thermal Conductivity:
- Steel has moderate thermal conductivity. While it can efficiently absorb heat, it does not dissipate it as quickly as C/C composites, which can lead to higher temperatures during intense braking.
Thermal Expansion:
- Steel exhibits higher thermal expansion compared to C/C composites. This can lead to dimensional changes under high heat, potentially affecting the fit and efficiency of brake components.
Ceramic (Used in Some High-Performance and Military Aviation Brakes)
High-Temperature Resistance:
- Ceramic materials are extremely resistant to high temperatures and maintain their properties even above 1,000 degrees Celsius.
Thermal Conductivity:
- Ceramics generally have lower thermal conductivity compared to metals and C/C composites. This means they are not as efficient at dissipating heat, which can result in higher operational temperatures.
Thermal Expansion:
- Ceramics have low thermal expansion, similar to C/C composites, which is beneficial for maintaining dimensional stability under thermal stress.
Summary
- Temperature Handling: C/C composites excel in environments where extremely high temperatures are common, outperforming both steel and ceramics in temperature resistance without degradation.
- Heat Dissipation: C/C composites are better at dissipating heat compared to ceramics and perform comparably to steel. This makes them more suitable for applications like aviation brakes where heat management is critical.
- Dimensional Stability: Both C/C composites and ceramics offer superior dimensional stability at high temperatures compared to steel, due to their lower thermal expansion rates.
Given these properties, C/C composites are often the preferred choice for high-performance and military aviation brake systems, where the ability to withstand and manage extreme heat and stress without losing performance is crucial. This makes them ideal for ensuring safety, reliability, and efficiency in critical aviation applications.
Charpter 3
How do carbon-carbon brake heat packs perform under extreme temperatures and pressures typical in aircraft operations?
Carbon-carbon (C/C) brake heat packs are engineered to excel under the extreme temperatures and pressures characteristic of aircraft operations, particularly during landing and takeoff. These conditions are among the most demanding for any braking system, and C/C composites are specially designed to handle these challenges. Here’s an overview of their performance under such conditions:
High-Temperature Performance
Exceptional Heat Tolerance:
- C/C composites can withstand temperatures up to 2,500 degrees Celsius. This capacity is crucial during aircraft operations where the brake system can reach extremely high temperatures due to the kinetic energy converted to thermal energy during rapid deceleration.
Thermal Stability:
- These materials maintain structural integrity and mechanical properties even at these high temperatures, ensuring that the brakes continue to function reliably without degradation.
Reduced Brake Fade:
- Brake fade, a reduction in braking power due to heat, is significantly minimized in C/C brake systems. Their ability to tolerate high temperatures and dissipate heat efficiently ensures consistent braking performance even under intense usage.
Performance Under High Pressure
Durability Under Load:
- Aircraft brake systems are subjected to enormous pressures from the weight and speed of the aircraft during landings. C/C composites are exceptionally strong in compression, able to withstand these pressures without fracturing or deforming.
Consistent Friction Coefficient:
- The frictional properties of C/C composites remain stable across a wide range of temperatures and pressures, unlike materials like steel or aluminum, which might exhibit varying friction coefficients under different operational conditions. This consistency is vital for predictable and reliable braking.
Longevity and Wear Resistance
Low Wear Rate:
- C/C composites exhibit a very low wear rate even under the severe conditions of aircraft braking. This contributes to longer lifespans of the brake discs and fewer replacements, which is cost-effective in the long run.
Resistance to Thermal Shock:
- Sudden changes in temperature can cause some materials to crack or warp. C/C composites resist such thermal shocks, maintaining their structure and performance even when cooling rapidly post-landing.
Overall Impact on Aircraft Operations
- Weight Reduction: Lighter than metal-based alternatives, C/C composites contribute to overall weight reduction in the aircraft, leading to better fuel efficiency and handling.
- Maintenance Reduction: The durability and resistance to wear of C/C composites mean that maintenance and replacement frequencies can be significantly reduced, enhancing operational readiness and reducing downtime.
In summary, carbon-carbon brake heat packs are particularly well-suited for the rigorous demands of aircraft operations. Their ability to perform under high temperatures and pressures, combined with their excellent wear resistance and thermal stability, make them ideal for ensuring safety and efficiency in aviation braking systems.
Charpter 4
What is the typical lifespan of a C/C brake heat pack in commercial and military aircraft?
The lifespan of carbon-carbon (C/C) brake heat packs in commercial and military aircraft can vary significantly based on several factors including the type of aircraft, usage patterns, operational environments, and maintenance practices. However, here are some general insights into their typical lifespan:
Commercial Aircraft
Lifespan Range:
- For commercial aircraft, C/C brake heat packs typically last between 1,000 to 3,000 landings. This range can be influenced by factors such as the size and weight of the aircraft, the typical runway length, and the specific landing conditions (e.g., hard versus soft landings).
Maintenance Practices:
- Regular maintenance and inspections are crucial. The actual lifespan can be extended with proper care and timely servicing, which includes regular checks for wear and damage, and replacing components before they fail.
Operational Conditions:
- Frequent short-haul flights with more takeoffs and landings can accelerate wear compared to long-haul flights. Additionally, operating in harsh environments, like very hot or cold climates, can also affect the durability of the brakes.
Military Aircraft
Lifespan Range:
- In military applications, the lifespan of C/C brake heat packs can be shorter due to the more demanding operational requirements. These brakes might endure anywhere from several hundred to over 1,000 landings, depending on the aircraft type and mission profile.
High-Performance Stress:
- Military aircraft often execute more aggressive maneuvers and landings at higher speeds or on shorter or rougher runways, increasing the stress on brake systems. The extreme operating conditions can thus lead to more frequent replacements.
Maintenance and Replacement:
- Military aircraft typically follow strict maintenance schedules to ensure optimal performance and safety. The brakes are checked regularly for any signs of wear or damage, and components are replaced as needed to maintain operational readiness.
Factors Influencing Lifespan
- Aircraft Type and Usage: Heavier aircraft or those that are frequently used may see quicker wear on brake systems.
- Landing Technique: Harder landings exert more force on the brakes, reducing their lifespan.
- Environmental Factors: Operations in environments with debris, dust, or corrosive elements (like saltwater airfields) can accelerate wear.
- Maintenance Quality: Consistent, high-quality maintenance can significantly prolong the life of C/C brake systems.
Overall, while C/C brakes are known for their durability and high performance, their lifespan in aviation contexts is heavily dependent on a combination of operational stresses and maintenance practices. Ensuring optimal performance involves regular monitoring and maintenance to adapt to the specific conditions under which the aircraft operates.
Charpter 5
How does the performance of C/C brake heat packs affect the overall safety and efficiency of an aircraft?
The performance of carbon-carbon (C/C) brake heat packs plays a crucial role in both the safety and efficiency of an aircraft. These advanced braking systems are designed to handle the extreme conditions of aviation operations, providing several key benefits that directly influence an aircraft’s operational capabilities.
Safety Enhancements
Reliable Performance Under High Temperatures:
- C/C brake heat packs maintain their structural integrity and functionality even at very high temperatures, which are common during intense braking on landing. This reliability ensures that the brakes will perform as expected every time, which is crucial for safe landings.
Consistent Braking Action:
- The consistent friction coefficients provided by C/C materials mean that pilots can expect predictable braking performance. This predictability is vital for safely managing landing distances and handling emergency or abrupt braking scenarios.
Resistance to Brake Fade:
- Brake fade, a reduction in braking effectiveness due to heat buildup, is significantly reduced with C/C brakes. This characteristic is particularly important during situations like repeated landings or when operating in hot climates, ensuring that the brakes remain effective throughout the operation.
High Wear Resistance:
- The superior wear resistance of C/C composites leads to less frequent brake malfunctions or failures. This durability is crucial for maintaining the safety and reliability of aircraft operations over time.
Efficiency Improvements
Weight Reduction:
- C/C materials are lighter than traditional metal brakes. This reduction in weight decreases the overall aircraft weight, which can lead to improved fuel efficiency, longer range, and better payload capacity.
Reduced Maintenance and Downtime:
- The longevity and durability of C/C brake heat packs mean that they require less frequent replacements and maintenance. This reliability can significantly reduce downtime for aircraft, leading to more efficient operations and lower maintenance costs.
Thermal Management:
- Effective heat dissipation by C/C brakes helps in managing the thermal loads on other nearby components, potentially reducing the risk of heat-related damage and the need for additional cooling systems, which can further reduce weight and complexity.
Operational Flexibility:
- The ability to perform effectively under various conditions allows aircraft equipped with C/C brakes to operate more flexibly, including at airports with shorter runways or those located in hot or high-altitude environments where thinner air can affect the performance of other brake types.
Overall Impact
The integration of C/C brake heat packs into aircraft systems directly enhances safety by providing reliable, consistent, and effective braking. Concurrently, the efficiency of operations is improved through reductions in operational weight, maintenance requirements, and broader operational capabilities. These factors make C/C brakes a preferred choice for modern aircraft, particularly those operating in demanding environments or requiring high performance. This integration not only boosts the aircraft’s performance but also contributes to economic benefits for airlines through reduced operational costs and improved service reliability.
Charpter 6
What is the initial cost comparison between carbon-carbon brake systems and traditional braking systems?
Carbon-carbon (C/C) brake systems generally have a higher initial cost compared to traditional braking systems, such as those made from steel or other metal alloys. Here’s a breakdown of the cost factors and a general comparison:
Initial Cost Factors for Carbon-Carbon Brake Systems
Material Costs:
- C/C composites are made from carbon fiber and carbon matrix, both of which are expensive materials. The production process for C/C composites is also more complex and energy-intensive, involving high-temperature treatment phases like carbonization and graphitization.
Manufacturing Complexity:
- The process to manufacture C/C brake systems is technologically advanced, requiring specialized equipment and controlled conditions. This complexity adds to the overall cost of the brake systems.
Research and Development:
- Significant investment in R&D is required to develop effective C/C brake systems, particularly to tailor them to specific applications like aerospace or high-performance automotive use. This cost is often reflected in the price of the final product.
Cost Comparison with Traditional Braking Systems
Steel or Iron Brakes:
- Traditional brakes, often made from steel or iron, are much less expensive to produce. The materials are readily available and cheaper, and the manufacturing processes are well-established and less energy-intensive.
Ceramic Brakes:
- Ceramic brakes, another high-performance option, are also generally cheaper than C/C brakes but more expensive than metal brakes. They provide some of the high-temperature performance advantages of C/C brakes but at a lower cost.
Economic Considerations
Long-Term Savings: Despite the higher initial costs, C/C brake systems can offer long-term savings due to their durability and low maintenance requirements. They tend to last longer than traditional brakes under high-performance conditions, reducing the frequency and associated costs of replacements.
Performance Efficiency: The improved performance and efficiency (e.g., better heat management and reduced weight) can translate into cost savings in operational terms, such as lower fuel consumption and fewer operational delays.
Typical Applications
Aviation and Motorsports: In sectors like aerospace and competitive motorsports, where performance and safety are paramount, the high initial cost of C/C brake systems is often justified. These sectors benefit significantly from the superior properties of C/C brakes, making them a worthwhile investment despite the higher upfront costs.
Consumer Automotive: For standard consumer vehicles, the cost-benefit ratio of using C/C brakes usually doesn’t justify the high initial expense, which is why these vehicles typically use metal or ceramic brakes.
In summary, while the initial cost of carbon-carbon brake systems is substantially higher than that of traditional braking systems, the investment is often justified in fields where performance, safety, and operational longevity are critical. These factors need to be considered when deciding whether the higher initial expense is warranted for a particular application.
Charpter 7
Are there long-term cost benefits associated with using C/C brakes in terms of maintenance, durability, and replacement frequency?
Yes, there are several long-term cost benefits associated with using carbon-carbon (C/C) brakes, particularly in terms of maintenance, durability, and replacement frequency. These benefits make C/C brakes an appealing investment despite their higher initial costs, especially in high-performance and critical applications like aviation and motorsports. Here’s how these benefits break down:
1. Maintenance Costs
- Lower Maintenance Needs: C/C brakes are less prone to wear and degradation under normal operating conditions, which reduces the frequency of maintenance checks and service requirements. This can result in significant savings, especially in professional settings where downtime for maintenance translates directly into operational costs.
- Simplified Maintenance Routines: Given their resistance to high temperatures and structural stability, C/C brakes often require less complex maintenance routines. This can reduce the labor time and costs associated with maintaining the braking system.
2. Durability
- Extended Lifespan: C/C brakes have a much longer lifespan compared to traditional steel or ceramic brakes, particularly under the high stress of extreme operating conditions. This durability means that the brakes need to be replaced less frequently, which can be a significant cost advantage over the life of the system.
- Consistent Performance: The ability of C/C brakes to maintain their performance characteristics over time, without significant deterioration, ensures that the efficiency and safety of the system are not compromised, reducing the potential costs related to performance-related failures or accidents.
3. Replacement Frequency
- Reduced Replacement Rate: C/C brake systems typically do not need to be replaced as often as their metal or ceramic counterparts. This can lead to cost savings not only on the materials and parts themselves but also on the labor costs associated with replacements.
- Predictable Replacement Scheduling: The wear and performance of C/C brakes can be more predictable, allowing for better planning and budgeting for replacements. This predictability helps in managing maintenance schedules and operational budgets more efficiently.
4. Operational Efficiency
- Weight Reduction: The lighter weight of C/C brakes contributes to overall vehicle efficiency, offering savings in fuel costs and potentially increasing payload capacity, which is particularly valuable in sectors like aviation.
- Improved Safety and Reliability: Enhanced safety and reliability reduce the risk of accidents and the associated direct and indirect costs, such as insurance premiums, liability, and potential downtime of vehicles or aircraft.
5. Total Cost of Ownership
- Long-Term Savings: When considering the total cost of ownership, which includes purchase price, maintenance, replacements, and operational impacts, C/C brakes can offer considerable long-term savings. These savings are especially pronounced in sectors where the brakes are subjected to extreme conditions that would rapidly degrade lesser materials.
In sectors where high performance and reliability are crucial, such as in military and commercial aircraft or high-performance automotive applications, the long-term cost benefits of C/C brakes can significantly outweigh their higher initial cost. This makes them a strategically advantageous choice for scenarios where performance, safety, and operational efficiency are top priorities.
Charpter 8
What are the maintenance requirements for C/C brake heat packs in aircraft?
Maintaining carbon-carbon (C/C) brake heat packs in aircraft is crucial for ensuring their performance and reliability. These brakes, known for their durability and efficiency under extreme conditions, still require specific care to operate optimally. Here’s an overview of the typical maintenance requirements for C/C brake heat packs in aviation:
1. Regular Inspections
- Visual Checks: Routine visual inspections are critical. Maintenance personnel look for signs of wear, surface damage, cracking, and any other structural changes in the brake discs and pads. These inspections often occur during regular aircraft maintenance schedules such as before flights or during more comprehensive checks.
- Thickness Measurement: The thickness of the brake discs and pads is checked to ensure they are within operational limits. Wear beyond specified tolerances requires part replacement to maintain braking efficiency and safety.
2. Detailed Examination
- Non-Destructive Testing (NDT): Techniques such as ultrasonic testing or radiography may be used to detect internal flaws or damages in C/C components that aren’t visible on the surface. This type of testing helps predict potential failures and ensures the integrity of the brake system.
- Thermal Imaging: Occasionally, thermal imaging might be used to assess the performance of the brake system post-flight to ensure even and appropriate heat distribution and dissipation, indicating good health of the brake system.
3. Performance Testing
- Brake Function Tests: Regular testing of brake functionality may be conducted on the ground to ensure that the brakes engage and release correctly and effectively under various simulated conditions.
- Wear and Performance Analysis: Data from the aircraft’s brake system can be analyzed to assess the performance over time and predict when maintenance or replacements might be needed.
4. Cleaning and Servicing
- Cleaning Procedures: Regular cleaning of the brake system is necessary to remove debris, dust, and any residues that might affect the performance of the brakes. Special solvents or cleaning agents designed for use with C/C materials are used to avoid damaging the composite material.
- Lubrication of Components: While C/C materials themselves do not require lubrication, associated components such as calipers and sliders may need regular lubrication to ensure smooth operation.
5. Replacement and Upkeep
- Scheduled Replacements: Based on the manufacturer’s recommendations and wear rates observed during inspections, parts of the brake system such as pads or discs may need scheduled replacements.
- Update Maintenance Records: Accurate and up-to-date maintenance records are vital for tracking the history and condition of each brake system component, aiding in predictive maintenance and compliance with aviation regulations.
6. Adherence to Regulatory Standards
- Regulatory Compliance: All maintenance work on aircraft C/C brakes must comply with aviation regulatory standards, which may vary by jurisdiction. These standards ensure that maintenance procedures meet safety and operational guidelines.
Training and Expertise
- Specialized Training: Technicians working on C/C brake systems should have specialized training given the critical nature and unique properties of these components. Understanding how to handle high-performance composite materials is essential for effective maintenance.
Regular and meticulous maintenance of C/C brake heat packs ensures their reliability and effectiveness in aircraft operations, ultimately contributing to the safety and performance of the aircraft. Proper care extends the lifespan of these components, making them a more cost-effective choice despite their higher initial investment.
Charpter 9
How frequently do C/C brake packs need to be inspected and replaced?
The inspection and replacement frequency of carbon-carbon (C/C) brake packs in aircraft can vary based on several factors, including the type of aircraft, the intensity of its use, and specific operating environments. However, general guidelines can be established to ensure optimal performance and safety.
Inspection Frequency
Routine Visual Inspections:
- Regular Flights: For commercial and general aviation, routine inspections might occur at scheduled maintenance intervals, such as every 100 flight hours or during A and B checks, which are typically conducted every few months.
- High-Performance Aircraft: In military or high-performance aircraft, inspections could be more frequent due to the demanding nature of operations.
Detailed Inspections:
- Detailed inspections, including measurements for wear and non-destructive testing (NDT), are usually conducted during more comprehensive maintenance checks such as C and D checks in commercial aviation. These might occur annually or biennially, depending on the aircraft’s operational schedule and the manufacturer’s maintenance program.
Replacement Frequency
General Replacement Guidelines:
- Commercial Aircraft: C/C brake packs in commercial aircraft might typically last between 1,000 to 3,000 landings, depending on factors such as aircraft weight, landing speed, runway conditions, and braking habits. This translates to replacements every few years for high-usage commercial jets.
- Military and High-Performance Aircraft: Due to more aggressive usage patterns, replacements might occur more frequently, potentially after several hundred to a thousand landings.
Wear and Performance-Based Replacement:
- Replacement of parts within the brake packs, like discs and pads, is often based on specific wear limits set by the manufacturer. Once these limits are reached, as determined during regular inspections, replacements are necessary to maintain braking effectiveness and safety.
- Performance issues noted during operation, such as increased stopping distances or reduced deceleration, can also trigger more immediate inspections and potential replacements.
Monitoring and Data Analysis
- Data-Driven Maintenance: Many modern aircraft are equipped with systems that continuously monitor the condition of various components, including brake systems. Data collected can help predict wear trends and optimize maintenance schedules, allowing for condition-based maintenance rather than strictly time-based schedules.
Environmental and Operational Considerations
- Harsh Environments: Operations in harsh environments (e.g., very cold, hot, or dusty conditions) might necessitate more frequent inspections and potentially earlier replacements due to accelerated wear or degradation of the brake materials.
Overall, the maintenance schedule for C/C brake packs should align with the aircraft manufacturer’s recommendations and regulatory requirements, and be adjusted based on operational data and experiences. Regular inspections and timely replacements are crucial to ensuring the safety and efficiency of aircraft operations.
Charpter 10
Are there any special handling or storage requirements for C/C brake systems?
Yes, carbon-carbon (C/C) brake systems, with their unique material properties, require specific handling and storage protocols to ensure their integrity and performance. These requirements are crucial to prevent damage and degradation during non-operational periods. Here’s a detailed overview of the special handling and storage requirements for C/C brake systems:
Handling Requirements
Care During Installation and Removal:
- C/C materials, while extremely durable under operational conditions, can be susceptible to damage from impacts or mishandling. Technicians should use caution to avoid dropping or striking the brake components during installation and removal.
Use of Proper Tools:
- Special tools designed for use with C/C composites should be used to prevent scratching or other surface damages. This includes using torque wrenches with proper settings to avoid over-tightening, which could induce stress fractures or other structural damages.
Cleanliness:
- Surfaces of C/C brakes should be kept clean from contaminants such as oil, hydraulic fluids, and debris. These substances can affect the friction properties of the brakes or potentially lead to surface degradation.
Storage Requirements
Controlled Environment:
- C/C brake systems should be stored in a controlled environment where temperature and humidity are regulated. Extreme temperatures and high humidity can affect the composite material, potentially leading to changes in its structural integrity or performance characteristics.
Protection from Contaminants:
- Storage areas should be clean and free of contaminants. Protective coverings are recommended to prevent dust, debris, and chemical exposure, which can corrode or otherwise damage the brake components.
Avoid UV Exposure:
- Long-term exposure to ultraviolet (UV) light can degrade carbon fibers and the resin matrix in C/C composites. Storing these components away from direct sunlight or using UV-protective coverings can help mitigate this risk.
Physical Protection:
- To prevent mechanical damage, C/C brake systems should be stored in a way that avoids pressure or weight being placed on them. They should not be stacked under heavy items, and sharp objects should be kept away to prevent scratching or puncturing.
Positioning:
- Ideally, C/C brake components should be stored in a stable position that distributes weight evenly and prevents warping or bending. For disc and pad storage, vertical positioning in specially designed racks can help maintain shape and condition.
Special Considerations
Handling by Trained Personnel:
- Only personnel trained in handling high-performance composite materials should manage the handling and storage of C/C brake systems to ensure proper procedures are followed.
Inventory Checks:
- Regular inventory checks and condition assessments should be conducted to ensure that stored components have not degraded or been compromised during storage.
By adhering to these handling and storage guidelines, the functional lifespan of C/C brake systems can be maximized, maintaining their high performance and safety characteristics when installed in aircraft or other high-demand applications.
Charpter 11
Which types of aircraft are most likely to benefit from carbon-carbon brake systems?
Carbon-carbon (C/C) brake systems offer exceptional performance characteristics that make them particularly well-suited for specific types of aircraft where reliability, efficiency, and performance under extreme conditions are paramount. Here are the types of aircraft that are most likely to benefit from incorporating C/C brake systems:
1. Commercial Airliners
- High Traffic and Frequent Landing: Large commercial airliners benefit from C/C brakes due to their frequent landing schedules, which require durable and reliable braking systems. The high wear resistance and ability to withstand repeated high thermal loads make C/C brakes ideal for these aircraft, ensuring safety and reducing maintenance downtime.
2. Military Aircraft
- Extreme Operational Demands: Military aircraft, which often perform at extreme limits, require brakes that can handle high speeds, aggressive maneuvers, and sudden stops. C/C brakes are perfect for these applications because of their high temperature and abrasion resistance, ensuring operational readiness and safety in critical situations.
3. Cargo Planes
- Heavy Loads: Cargo planes, which carry variable and often very heavy loads, need reliable braking systems that can consistently perform under heavy weight. The strength and low wear rates of C/C brake systems are beneficial for handling the additional stress during landings.
4. Business Jets
- Performance and Luxury: Business jets often operate out of smaller airports with shorter runways, necessitating efficient and reliable braking systems. C/C brakes provide the necessary performance, enabling these jets to land safely in limited spaces while offering the reduced maintenance and longer lifecycle that suit the luxury and business aviation markets.
5. Supersonic Jets
- High-Speed Operations: Aircraft designed to operate at supersonic speeds experience extreme thermal and mechanical stresses on their braking systems during landings. The superior thermal resistance and stability of C/C brakes make them an essential choice for these high-speed aircraft.
6. Spacecraft
- Reentry and Landing: Spacecraft and reusable launch vehicles, such as those used in space programs, benefit from C/C brake systems during reentry and landing phases. The ability of C/C brakes to withstand the extreme temperatures and conditions encountered during atmospheric reentry is crucial for the safety and reusability of space vehicles.
Benefits of C/C Brakes in Aviation
- Safety: Enhanced safety due to reliable performance in critical landing conditions and high-stress environments.
- Cost-Effectiveness: Although more expensive initially, the long lifespan and reduced maintenance needs provide cost savings over time.
- Efficiency: The lightweight nature of C/C materials contributes to overall fuel efficiency and handling performance.
In summary, C/C brake systems are particularly beneficial for aircraft that operate under high-stress conditions, require high reliability, and where safety and performance are critical. Their use in commercial, military, and specialty aviation underscores their importance in modern aerospace applications.
Charpter 12
Are C/C brakes more suitable for military, commercial, or private aircraft, and why?
Carbon-carbon (C/C) brakes are highly suitable for various types of aircraft, each benefiting from the specific properties of C/C materials in different ways. The suitability often depends on the operational demands, performance requirements, and economic factors associated with each aircraft type. Here’s a detailed breakdown:
Military Aircraft
- Extreme Conditions: Military aircraft frequently operate in extreme conditions, including high-speed landings, aggressive takeoffs, and operations from austere runways. C/C brakes are ideal because they can withstand high temperatures and pressures, providing reliable performance where it’s crucial for mission success.
- Durability and Performance: The high durability and low maintenance requirements of C/C brakes are beneficial for military operations, reducing downtime and ensuring availability.
- Safety and Reliability: Military operations require uncompromised safety and reliability, which C/C brakes offer due to their superior thermal stability and consistent braking performance.
Commercial Airliners
- Frequent Use: Commercial airliners undergo numerous takeoffs and landings, often in quick succession, which generates significant heat in the brake system. C/C brakes’ ability to resist high temperatures and thermal degradation makes them excellent for handling the rigorous braking schedule without compromising performance or safety.
- Economic Efficiency: Although C/C brakes have a higher upfront cost, their longer lifespan and reduced maintenance frequency can offer cost savings over time, particularly for high-utilization commercial fleets.
- Weight Reduction: The lightweight nature of C/C brakes contributes to overall fuel efficiency—an important consideration for commercial airlines operating under tight operational budgets and environmental regulations.
Private Aircraft
- Performance Requirements: Private aircraft, especially high-performance jets, benefit from the enhanced capabilities of C/C brakes, which provide reliable stopping power in a variety of runway conditions and contribute to the aircraft’s overall agile performance.
- Space and Weight Savings: The compact and lightweight characteristics of C/C brakes are particularly advantageous in smaller aircraft, where every kilogram saved can significantly impact performance and fuel efficiency.
- Longevity: Owners of private aircraft may also appreciate the longer intervals between brake replacements and maintenance checks that C/C brakes allow, aligning with the lower usage rates typical of private aviation.
Suitability Comparison
- Military Aircraft: Perhaps the most suited due to the demanding operational requirements and the need for absolute reliability in critical situations.
- Commercial Airliners: Also highly suitable, especially for long-haul and large aircraft that benefit from the extended lifespan and reduced maintenance needs, balancing the initial higher costs with long-term operational savings.
- Private Aircraft: Suitable particularly for high-performance and luxury jets where cost is less of a constraint and performance and weight advantages are prioritized.
In summary, while C/C brakes are exceptionally well-suited for military applications due to their performance under extreme conditions, commercial and private aircraft also benefit significantly from the advanced properties of C/C brakes. The choice often hinges on balancing the initial investment against the benefits of durability, safety, performance, and maintenance savings.
Charpter 13
What are the challenges involved in retrofitting existing aircraft with carbon-carbon brake systems?
Retrofitting existing aircraft with carbon-carbon (C/C) brake systems involves a series of challenges, mainly due to the differences in material properties, system requirements, and integration complexities between C/C brakes and traditional braking systems. Here’s an outline of the primary challenges involved in such retrofit projects:
1. Compatibility Issues
- System Integration: C/C brake systems might require different supporting infrastructure compared to traditional metal brakes. For instance, the hydraulic systems, actuators, and sensors might need adjustments or replacements to handle the specific characteristics of C/C brakes, such as their operating pressures and temperatures.
- Wheel and Landing Gear Compatibility: The existing wheel assemblies and landing gear may need modifications to accommodate C/C brake systems, which could have different dimensions or mounting requirements compared to original equipment.
2. Certification and Regulation
- Airworthiness Certification: Any modification to aircraft systems, including brakes, must meet stringent regulatory standards. Obtaining certification for a retrofit involves extensive testing and validation to prove that the new system is at least as safe and effective as the one it replaces.
- Compliance with Standards: Ensuring that the retrofit meets all relevant aviation standards and regulations can be a complex and time-consuming process, requiring collaboration with regulatory bodies and possibly extensive documentation and reporting.
3. Cost Considerations
- Initial Investment: The upfront cost of C/C brakes is higher than traditional brakes. When retrofitting, this cost is compounded by the need for additional components, system modifications, and the labor involved in the installation.
- Cost-Benefit Analysis: Airlines or aircraft operators must evaluate the long-term benefits of retrofitting C/C brakes against the initial costs. While C/C brakes offer advantages in terms of maintenance and operational efficiency, the investment must be justifiable over the aircraft’s remaining service life.
4. Technical Expertise
- Installation Complexity: Retrofitting a brake system is not a straightforward task and requires high technical expertise. The personnel involved need specific training and knowledge about C/C materials and the particular systems of the aircraft being retrofitted.
- Maintenance Training: Maintenance crews must be trained not only on the installation but also on the ongoing maintenance and inspection requirements of the new brake system, which differ from those of traditional brakes.
5. Operational Testing
- Performance Testing: After installation, comprehensive ground and flight testing are necessary to ensure the system performs as expected under various operating conditions. This testing can be resource-intensive and requires careful planning and execution.
- Adjustments and Tweaking: It’s likely that some issues will only become apparent during these tests, requiring further adjustments and potential redesigns of some components.
6. Logistics and Downtime
- Aircraft Downtime: Retrofitting brake systems can lead to significant downtime for the aircraft, which means a loss of revenue during the period when the aircraft is out of service.
- Scheduling and Planning: Effective project management is required to minimize downtime and integrate the retrofit into the aircraft’s regular maintenance schedule to avoid additional disruptions.
Retrofitting aircraft with C/C brake systems, while offering significant long-term benefits, poses substantial challenges that must be carefully managed to ensure success. Thorough planning, expert execution, and adherence to regulatory requirements are essential to overcoming these challenges and achieving a successful integration of C/C brakes into existing aircraft fleets.
Charpter 14
Are carbon-carbon brake systems compatible with all types of aircraft wheels and tires?
Carbon-carbon (C/C) brake systems are not universally compatible with all types of aircraft wheels and tires without some modifications or considerations. Their compatibility largely depends on the specific design and requirements of the aircraft’s wheel and tire assembly, as well as the operating conditions expected. Here are some key factors that influence this compatibility:
1. Design Specifications
- Wheel Size and Configuration: C/C brake systems have specific dimensional and mounting requirements that may differ from those of traditional brake systems. Aircraft wheels must have the appropriate size and configuration to house C/C brake discs and calipers, which can sometimes be larger or shaped differently than conventional metal brakes.
2. Thermal Characteristics
- Heat Dissipation Needs: C/C brakes are designed to operate at much higher temperatures than standard metal brakes. This high heat generation requires compatible wheel materials that can withstand these temperatures without deforming or failing. Some wheel materials, particularly certain alloys used in lighter aircraft, might not tolerate the intense heat as well.
3. Load Distribution
- Structural Stress Handling: The wheel assembly must be robust enough to handle the different stress distribution characteristics of C/C brakes, which may exert different forces on the wheel due to their lighter weight and higher performance capabilities.
4. Tire Compatibility
- Heat Effects on Tires: The increased heat production of C/C brakes can also impact tire performance. Tires need to be capable of withstanding higher temperatures without degradation of rubber compounds. Aviation tires are generally designed to endure significant heat, but the additional heat from C/C brakes may require tires with higher heat tolerance.
5. Modification Requirements
- Retrofitting Challenges: In cases where an aircraft is being retrofitted with C/C brakes, it may require modifications to the existing wheel assemblies. This could involve changing the wheel material, redesigning the wheel structure, or updating other brake system components like hydraulic lines and sensors to ensure full system integration and functionality.
6. Certification and Safety Standards
- Regulatory Compliance: Any changes to wheel and brake assemblies must meet strict aviation safety and performance standards. Certification of the new assembly is required to demonstrate that the integration of C/C brakes with existing or modified wheels meets these standards.
Conclusion
While C/C brake systems offer superior performance, especially in high-demand aviation environments, their integration into an aircraft’s wheel and tire system must be carefully evaluated and often specifically engineered. Compatibility is not guaranteed across all aircraft types without appropriate modifications and adjustments. Ensuring that all components work harmoniously is crucial for maintaining safety and performance standards in aviation.
Charpter 15
What are the certification processes required for integrating C/C brake systems into existing aircraft models?
Integrating carbon-carbon (C/C) brake systems into existing aircraft models involves a detailed certification process to ensure that the new systems meet rigorous safety and performance standards. This process is governed by aviation regulatory bodies such as the Federal Aviation Administration (FAA) in the United States, the European Union Aviation Safety Agency (EASA) in Europe, and other similar organizations worldwide. Here’s an overview of the typical steps involved in the certification process for retrofitting aircraft with new brake systems:
1. Design and Development
- Engineering Analysis: This includes a detailed analysis of the design and performance specifications of the C/C brake system. The compatibility with the existing aircraft model must be thoroughly evaluated in terms of fit, operational impact, and safety.
- Prototype Development: Often, a prototype of the C/C brake system is developed and tested to ensure that it meets the initial design requirements.
2. Testing and Validation
- Bench Testing: Before flight testing, the C/C brake system undergoes rigorous bench testing to validate its performance under various conditions. This includes tests for endurance, temperature resistance, stress limits, and other critical performance metrics.
- Flight Testing: The brake system is then installed on a test aircraft to evaluate its performance in actual flight conditions. This testing is crucial to observe the system’s behavior under operational stresses and real-world scenarios.
3. Documentation and Reporting
- Detailed Documentation: Comprehensive documentation of the testing procedures, results, and analyses is compiled. This documentation must include all engineering data, test results, safety analyses, and proof of compliance with all relevant standards.
- Submission to Regulatory Bodies: The complete package is submitted to the relevant aviation regulatory authority for review. This submission must convincingly demonstrate that the C/C brake system meets or exceeds all existing safety and performance standards for the aircraft type.
4. Regulatory Review and Approval
- Review Process: The regulatory authority reviews the submitted documents and test results. This review process may involve questions, requests for additional data, or further testing to clarify or confirm certain aspects.
- Certification Issuance: If the regulatory body is satisfied that the new brake system is safe and compliant with all standards, they will issue a Supplemental Type Certificate (STC) or a similar certification. This certificate allows the C/C brake system to be installed on the aircraft models specified in the application.
5. Implementation and Continued Oversight
- Installation on Fleet: With the certification in hand, the new C/C brake systems can be installed across the fleet. All installations must comply with the specifics of the certification to ensure safety and legality.
- Post-Implementation Monitoring: After integration, ongoing monitoring and reporting are required to ensure that the system continues to perform as expected. Any incidents or unexpected behaviors must be reported to the regulatory authorities.
6. Training and Documentation
- Maintenance and Operational Training: It’s crucial that all operational and maintenance staff are fully trained on the new C/C brake systems. This includes understanding the differences in handling, maintenance requirements, and emergency procedures.
- Update of Operational Manuals: All relevant aircraft and maintenance manuals must be updated to include information on the new brake systems, ensuring that all information is readily available for operational and safety compliance.
The certification process is thorough and designed to ensure that any new system integrated into an aircraft does not compromise safety. This rigorous procedure is essential for maintaining the high safety standards required in aviation.
Charpter 16
Are there specific aviation regulations that affect the use of carbon-carbon brake systems?
Yes, the use of carbon-carbon (C/C) brake systems in aviation is subject to specific regulations that ensure their safety, reliability, and performance. These regulations are set by aviation authorities such as the Federal Aviation Administration (FAA) in the United States, the European Union Aviation Safety Agency (EASA) in Europe, and other national and international regulatory bodies. The regulations cover a wide range of requirements, from the certification and maintenance of the brakes to their operational usage. Here are some of the key areas where aviation regulations affect the use of C/C brake systems:
1. Certification Requirements
- Airworthiness Certification: C/C brake systems must meet stringent airworthiness standards to be certified for use. This involves thorough testing to demonstrate that the brakes perform safely under expected operating conditions and all foreseeable emergency scenarios.
- Supplemental Type Certificates (STC): For retrofitting existing aircraft with C/C brakes, an STC is often required. This certificate proves that the retrofit meets the same safety and performance standards as the original equipment.
2. Design and Manufacturing Standards
- Quality Assurance: Manufacturing processes for C/C brake systems must adhere to quality standards that ensure every unit is consistent and reliable. This includes detailed records of materials, production processes, and quality control measures.
- Design Standards: The design of C/C brake systems must comply with established standards for durability, reliability, and functionality. These standards help ensure that the brakes will perform effectively in the diverse and demanding conditions faced by different types of aircraft.
3. Maintenance and Inspection Regulations
- Regular Inspections: Regulations specify how often C/C brake systems must be inspected, what aspects must be checked, and which methodologies should be used (e.g., visual inspections, non-destructive testing).
- Maintenance Procedures: Detailed maintenance procedures are mandated to ensure that all actions taken on the brakes are safe, effective, and appropriate. This includes guidelines on how to handle wear limits, replacement schedules, and unexpected repairs.
4. Operational Use
- Operational Limits: There may be regulations that limit how and when C/C brakes can be used, such as during certain types of operations or in specific environmental conditions. These limits help ensure that the brakes are only used within the parameters for which they have been tested and certified.
- Training Requirements: Pilots and maintenance crews must receive specific training on the characteristics and requirements of C/C brake systems. This ensures that all personnel are knowledgeable about how these systems differ from more traditional braking solutions.
5. Reporting and Documentation
- Incident Reporting: Aviation regulations require the reporting of any failures or irregularities in brake performance. This helps regulatory bodies monitor the real-world effectiveness of C/C brakes and intervene if a pattern of issues emerges.
- Documentation Requirements: Detailed records of the installation, maintenance, and inspection of C/C brakes must be kept. These records ensure that an aircraft’s braking system can be audited and reviewed by regulatory authorities at any time.
Conclusion
The specific regulations governing C/C brake systems in aviation are designed to ensure that these advanced materials can be used safely and effectively. Compliance with these regulations is crucial for manufacturers, airlines, and maintenance organizations. It guarantees that the benefits of C/C brakes—such as superior performance, reduced weight, and lower maintenance needs—do not compromise the safety and reliability essential in the aviation industry.
Charpter 17
What are the latest developments in carbon-carbon brake technology for aircraft?
Carbon-carbon (C/C) brake technology for aircraft continues to evolve with advancements focused on improving performance, durability, and cost-effectiveness. These developments aim to address the growing demands of modern aviation, including the need for lighter, more reliable, and higher-performing braking systems. Here are some of the latest developments in C/C brake technology:
1. Material Enhancements
- New Composite Formulations: Researchers are developing new formulations of the carbon matrix and carbon fibers to enhance the mechanical properties and thermal resistance of C/C brakes. These new composites may offer better wear resistance and higher thermal stability, which can extend the life of the brakes and improve safety.
- Surface Treatments: Advances in surface treatments and coatings are being explored to increase the friction coefficient at lower temperatures and improve the overall performance across a wider range of operating conditions.
2. Manufacturing Innovations
- Automated Lay-up Techniques: Automation in the lay-up processes for C/C composites is helping to reduce manufacturing costs and improve the consistency of brake components. These automated techniques also allow for more complex geometries to be produced more reliably.
- 3D Printing of Carbon Composites: The use of additive manufacturing, or 3D printing, is emerging as a method to create more intricate composite structures. This technology could lead to lighter and more optimized brake designs by allowing for geometry that is impossible with traditional manufacturing methods.
3. Heat Management Improvements
- Enhanced Cooling Designs: Improved designs in the brake system architecture are focusing on enhancing heat dissipation capabilities. This includes optimized venting and heat sink designs that can more effectively manage the high temperatures generated during braking.
- Integration with Thermal Sensors: Advanced sensor technologies are being integrated into C/C brake systems to provide real-time monitoring of temperatures and wear levels. This data can be used to optimize braking performance and predict maintenance needs more accurately.
4. Regenerative Braking Systems
- Hybrid Systems: There’s increasing interest in integrating regenerative braking systems, which are common in electric and hybrid vehicles, into aircraft. These systems can help reduce the load on traditional brakes and improve overall efficiency by converting some of the kinetic energy into electrical energy, which can then be reused.
5. Sustainability Focus
- Recycling Processes: As the aviation industry continues to focus on reducing its environmental footprint, the development of recycling processes for C/C materials is becoming more critical. Efforts are underway to find cost-effective ways to recycle used C/C brake materials into new products.
6. Customization for Diverse Aircraft Needs
- Tailored Solutions: Advances in simulation and modeling technologies are allowing manufacturers to tailor C/C brake systems more precisely for specific aircraft performance requirements. This customization ensures that each aircraft model has brakes optimized for its particular size, weight, and operational profiles.
Conclusion
These developments reflect the ongoing innovation within the aerospace industry to meet the challenges of safety, efficiency, and environmental responsibility. As technology advances, C/C brake systems continue to set the standard for high-performance braking solutions in the demanding field of aviation.
Charpter 18
How is the technology evolving to meet the changing demands of the aviation industry?
The technology within the aviation industry is rapidly evolving to meet new demands for safety, efficiency, sustainability, and performance. Advances are being driven by the need to address environmental concerns, enhance operational capabilities, and improve economic viability. Here are key areas where aviation technology is evolving:
1. Fuel Efficiency and Emissions Reduction
- New Engine Technologies: Developments in engine design, such as geared turbofan engines and more efficient turbojets, are significantly reducing fuel consumption and emissions. These engines also reduce noise, which is a crucial factor in operating in noise-sensitive areas.
- Alternative Fuels: Research and implementation of sustainable aviation fuels (SAFs) derived from bio-based resources are on the rise. These fuels aim to reduce carbon footprints without requiring significant changes to existing aircraft engines and infrastructure.
2. Electrification of Aircraft
- Electric and Hybrid Propulsion Systems: The development of fully electric and hybrid-electric propulsion systems is progressing, aimed at reducing or even eliminating the reliance on fossil fuels. These technologies are particularly promising for short-haul flights and are expected to revolutionize urban air mobility.
- Energy Storage Improvements: Advances in battery technology are crucial for the feasibility of electric aircraft. Increased energy density, faster charging times, and enhanced safety are areas of intense development.
3. Autonomous and Unmanned Aircraft
- Autonomous Flight Technologies: Innovations in sensor technology, artificial intelligence, and machine learning are paving the way for increased automation in aircraft. This includes unmanned aerial vehicles (UAVs) for cargo and potentially passenger transport, as well as pilot-assist features in commercial aviation.
- Regulatory Developments: As autonomous technologies advance, regulatory bodies are working to establish frameworks that ensure these systems are as safe, if not safer, than manned operations.
4. Advanced Materials and Manufacturing Techniques
- Composite Materials: The use of advanced composite materials in airframe and engine construction continues to grow. These materials offer high strength-to-weight ratios, enhancing the aircraft’s performance and fuel efficiency.
- Additive Manufacturing (3D Printing): This technology is increasingly used to produce complex aircraft components more efficiently and with less waste. It allows for lighter and more optimized part designs that were previously impossible to create.
5. Digitalization and Connectivity
- Internet of Things (IoT): Aircraft are becoming more connected, with onboard sensors and systems continually collecting data on everything from engine performance to passenger comfort. This data can be used to optimize operations, predict maintenance needs, and enhance the overall travel experience.
- Cybersecurity: With increased connectivity comes the need for robust cybersecurity measures to protect aircraft systems and passenger data from cyber threats.
6. Enhanced Safety Technologies
- Collision Avoidance Systems: Advances in radar and communication technologies are improving the effectiveness of collision avoidance systems. These systems are essential as skies become more crowded with both traditional aircraft and drones.
- Advanced Weather Prediction Tools: Real-time data processing and improved predictive models are helping pilots better navigate around severe weather, increasing safety and reducing flight delays.
7. Sustainability Practices
- Reducing Environmental Impact: Beyond fuel efficiency, the industry is focusing on reducing the lifecycle environmental impacts of aircraft, including manufacturing and end-of-life recycling.
- Noise Reduction Technologies: Efforts to reduce the noise footprint of aircraft operations are ongoing, with new engine designs and operational strategies that minimize noise during takeoff and landing.
The evolution of technology in the aviation industry reflects a comprehensive approach to addressing the multifaceted challenges of modern air travel and transport. These innovations not only aim to enhance operational efficiency and safety but also strive to meet stricter environmental standards and adapt to changing economic conditions.
Charpter 19
What is the environmental impact of manufacturing and disposing of carbon-carbon brake systems compared to other materials?
The environmental impact of manufacturing and disposing of carbon-carbon (C/C) brake systems involves several factors, from the energy-intensive production processes to the challenges of recycling the materials used. When comparing C/C composites to other materials like steel or aluminum typically used in brake systems, different environmental footprints emerge based on material extraction, production, usage, and end-of-life management. Here’s a breakdown of these factors:
Manufacturing Impact
Energy Consumption:
- C/C Composites: The production of C/C brake systems is highly energy-intensive. Manufacturing involves the carbonization of polyacrylonitrile (PAN) fiber and subsequent graphitization at temperatures above 2000°C. These processes require significant amounts of energy, contributing to higher greenhouse gas emissions compared to more conventional materials.
- Steel/Aluminum: While the production of steel and aluminum is also energy-intensive and generates a considerable amount of CO2, the temperatures and energy required are generally lower than those needed for producing C/C composites.
Resource Extraction:
- C/C Composites: The production of the precursor materials for C/C composites, especially PAN, involves petrochemical derivatives, which have their own environmental impacts related to oil extraction and processing.
- Steel/Aluminum: The extraction of iron ore and bauxite (for aluminum) has significant environmental impacts, including habitat destruction, groundwater pollution, and energy consumption. However, both steel and aluminum are highly recyclable, which can mitigate some of these impacts over multiple life cycles.
Usage Impact
- Performance Efficiency: C/C brakes offer superior performance, especially in high-demand applications such as aviation and motorsports, leading to potential safety and efficiency benefits during use. The higher durability and efficiency can translate into less frequent replacements and potentially lower material usage over time.
End-of-Life Impact
Recyclability:
- C/C Composites: One of the major environmental drawbacks of C/C composites is their limited recyclability. The cross-linked structure of carbon fibers embedded in a carbon matrix is challenging to break down and reuse, leading to most spent C/C materials ending up in landfills.
- Steel/Aluminum: Both materials are highly recyclable with established recycling streams. Steel, for example, can be continuously recycled without degradation of its properties, which significantly reduces its environmental impact per unit of material over its lifecycle.
Disposal Issues:
- C/C Composites: The disposal of C/C composites poses challenges not only due to their non-biodegradability but also due to the lack of efficient processes for breaking down the material for reuse. Research into better recycling techniques is ongoing.
- Steel/Aluminum: These metals are often easier to deal with at the end of life due to the maturity of metal recycling technologies and infrastructures.
Overall Environmental Impact
While C/C brake systems offer performance advantages that can translate into safety and operational efficiency benefits, their environmental impact is generally higher in terms of both energy consumption during production and challenges at the end of life due to their recyclability issues. In contrast, traditional materials like steel and aluminum, despite their own significant impacts during extraction and production, offer better sustainability profiles in terms of recyclability and lifecycle management. The aviation and automotive industries are aware of these issues and are exploring ways to reduce the impacts through innovations in material science and recycling technologies.
Want us to develop carbon carbon brake applications for you new project?
Your aircraft model is not in the list?
You have any special requirements for the carbon carbon materials?