What Products do we supply?
We understand that exploring all aspects of our carbon matrix applications can be complex, so we’ve organized everything into easy-to-navigate sections. Use the content directory below to jump straight to the information you’re looking for.
Customized Carbon Matrix applications to Your Projects
At CMCMAT, we’re proud to offer a full range of Carbon Matrix composite customization services. With our advanced facilities and experienced team, we ensure that every client’s needs are met with the highest level of precision and quality. Here’s what we can offer you:

- Solar Photovoltaic Industry: C/C insulation sleeve, C/C guide tube,C/C heater, ovens etc.
- Aviation & Aerospace: C/C brake heat pack, Aircraft steel brakes, Rocket Nozzles ect.
- Automotive: C/C brake discs, C-C/SiC brake discs, brake pads etc.
- Defense and Military: Ballistic protection, Amor systems ect.
- Energy Industry: Nuclear reactors require resistance to radiation damage and high temperatures.
- Marine braking systems: Used in high-performance marine applications for braking systems, ensuring durability and resistance to saltwater corrosion.
Both carbon-carbon composites and carbon-ceramic composites play crucial roles in a wide range of industries, thanks to their outstanding mechanical properties, thermal stability, wear resistance, and lightweight nature. The aerospace, automotive, and defense industries are the primary fields that rely on these composites, but their applications extend across many sectors including energy, industrial, sports, electronics, and marine industries. As demand for high-performance materials continues to grow, the use of these advanced composites will only increase, providing durable, efficient, and innovative solutions to modern challenges
Key Features and Applications of Our Carbon Composite Products and Solutions

2.5D/ 3D Carbon fiber preforms
- 2.5D carbon fiber brake parts prefrom
- Carbon Fiber Quasi-3D Braided Textile Architecture Preform
- 3D Braided Carbon Fiber Textile Architecture Preform
- Hybrid 2.5D preform of quartz fiber/ PAN-based carbon fiber or pitch-based carbon fiber/ PAN-based carbon fiber
- Pre-oxidized fiber or pre-oxidized fiber/ PAN-based carbon fiber 2.5D preform
CMCMAT specializes in manufacturing 2.5D/3D structural preforms, directly fabricated from continuous fibers. By utilizing diverse fiber types, we tailor preform geometries to meet specific requirements. These high-performance preforms serve critical applications across industries such as automotive, aerospace, aviation, and thermal management systems, including: high-temperature resistant components; thermal insulation solutions; brake material blanks; advanced industrial composites.

High density Carbon Carbon Composite
- Cras ultricies mid
- Cras ultricies middg
- Cras ultricies mid ultricies
- Cras ultricie
Nunc interdum lacus sit amet orci. Aenean vulputate eleifend tellus. Aliquam erat volutpat. Suspendisse nisl elit, rhoncus eget, elementum ac, condimentum eget, diam. Quisque libero metus, condimentum nec, tempor a, commodo mollis, magna.
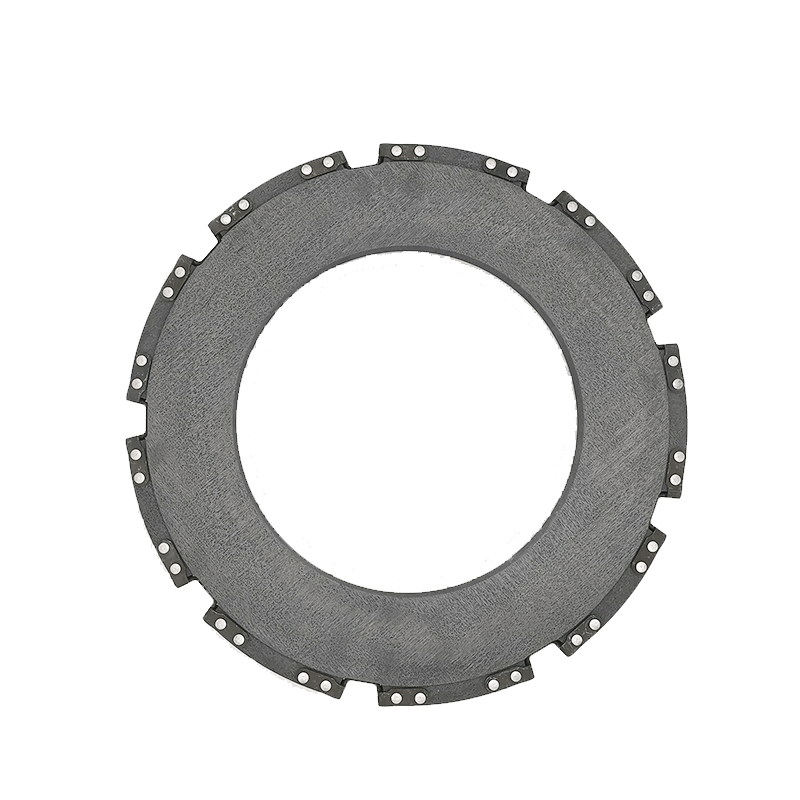
Aircraft brake heat packs
- Carbon Carbon, Carbon Ceramic and Steel material available
- PMA approval
- Heat packs for different aircraft types
- Ability for customization and develop heat packs
We offer a range of high-performance braking materials, including carbon-carbon (C/C), carbon-ceramic (C/SiC), and steel-based solutions. Select civil components are CAAC-PMA certified, ensuring compliance with stringent aviation safety standards. Designed for critical thermal management, our brakes deliver consistent performance across mission-critical aerospace and defense platforms, like UAV, civil planes and military jets.
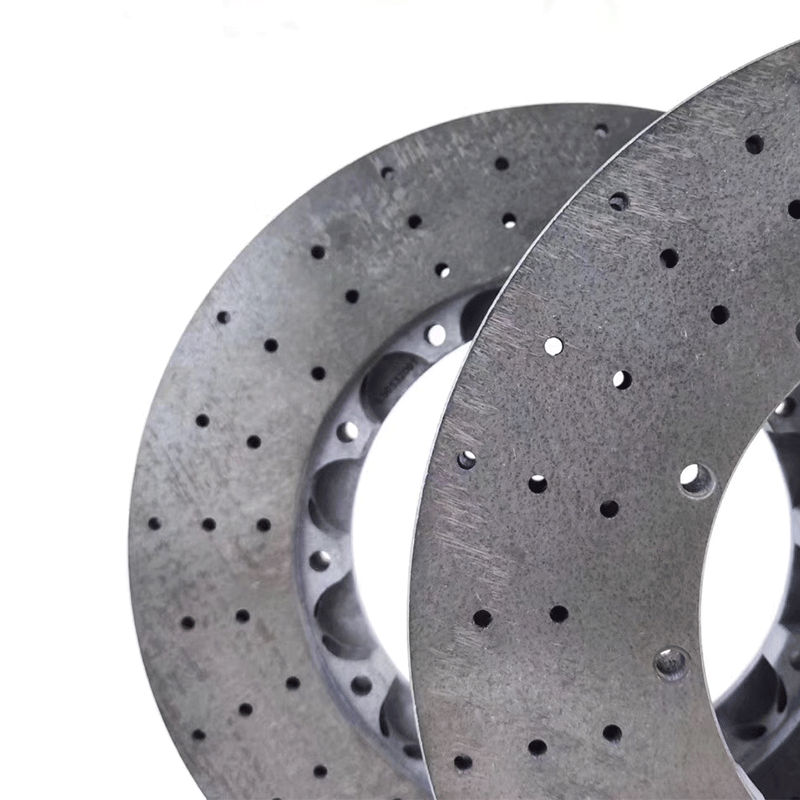
Carbon ceramic brake rotors
- Light weight
- No heat fade
- Long life-span
- Matching brake pads available
The automotive brakes we supplied are mainly carbon ceramic brakes. Carbon ceramic brakes are popular in track and street running. Customers can choose different brake pad compounds for different use.

Motorbike brake discs
- Carbon Carbon and Carbon ceramic options
- 220mm OD to 330mm OD
- For racing and GT roadokk
- Customization available
We also have carbon carbon clucth plates, carbon ceramic motorbike brake rotors, carbon carbon bolts and nuts etc.

Other carbon parts
- Carbon carbon and carbon ceramic options
We have the ability to customize the carbon carbon or carbon ceramic applications based on your detailed requirments.
Here is the video how we develop the carbon carbon or carbon ceramic brake discs
- Making carbon fiber preforms from continuous carbon fibers.
- Carbonnization the carbon fiber prefroms to carbon carbon composite.
- Machining the carbon carbon parts to needed shapes.
- Desification or ceramization the machined carbon carbond discs to C/C or C/C-SiC discs.
- Test the brake disc on the dyno.
- Test the brake disc on track.
What's the Difference between Carbon Carbon and Carbon Ceramic Composite?
Carbon-Carbon
Composition: Carbon-carbon is a composite material consisting of carbon fiber reinforcement in a matrix of graphite. The entire structure is carbon, which is why it is referred to as carbon-carbon.
Properties:
- High Temperature Resistance: It can withstand extremely high temperatures without losing strength, making it ideal for applications such as aircraft brake systems and space vehicles.
- Strength and Durability: Offers excellent structural strength and stiffness.
- Low Thermal Expansion: Exhibits minimal expansion when exposed to high temperatures, maintaining structural integrity.
Applications: Due to its high-cost and complex manufacturing process, it’s typically used in specialized applications such as aerospace (rocket nozzles, heat shields), motorsports, and military.
Carbon Ceramic
Composition: Carbon ceramic materials, or ceramic matrix composites, are made from silicon carbide ceramic reinforced with carbon fibers. They are manufactured through a process that combines carbon fiber with silicon to produce a material that offers the benefits of both ceramic and carbon.
Properties:
- Thermal Shock Resistance: Exhibits excellent resistance to sudden changes in temperature, which can be crucial in braking systems.
- Wear Resistance: Provides superior wear resistance compared to traditional materials like iron or steel.
- Lightweight: Significantly lighter than metals, contributing to improved vehicle efficiency and performance.
Applications: Primarily used in the automotive industry for brake discs and pads in high-performance and luxury vehicles due to their ability to provide superior braking performance with less wear and resistance to high temperatures.
Key Differences
- Heat Tolerance: Carbon-carbon can handle higher temperatures compared to carbon ceramic.
- Cost and Manufacturing: Carbon-carbon is more expensive and complex to manufacture.
- Typical Use Cases: Carbon-carbon is more common in aerospace and racing due to its extreme heat tolerance, while carbon ceramic is widely used in automotive applications for its balance of performance, durability, and cost.
Each type of material offers specific advantages that make it suitable for different applications, particularly where high performance and durability under extreme conditions are required.