Carbon Fiber Preforms

What kind of preforms we can supply?
3D/2.5D Needled Carbon Fiber Preforms
- 70% continuous carbon fibers and 30% felt cut and carding with continuous fibers
- The fibers are 3D needled to be a be a preform
- A 3D preform leads to higher shearing strength
- Easy to be customized as any shape
- We don’t use any molds in the full the process
- Highly benefit to the CVI/ CVD process when producing the carbon composites
- Any density in the range from 0.4 g/cm³ to 1.4 g/cm³ are avaliable

2.5D carbon fiber brake material preform
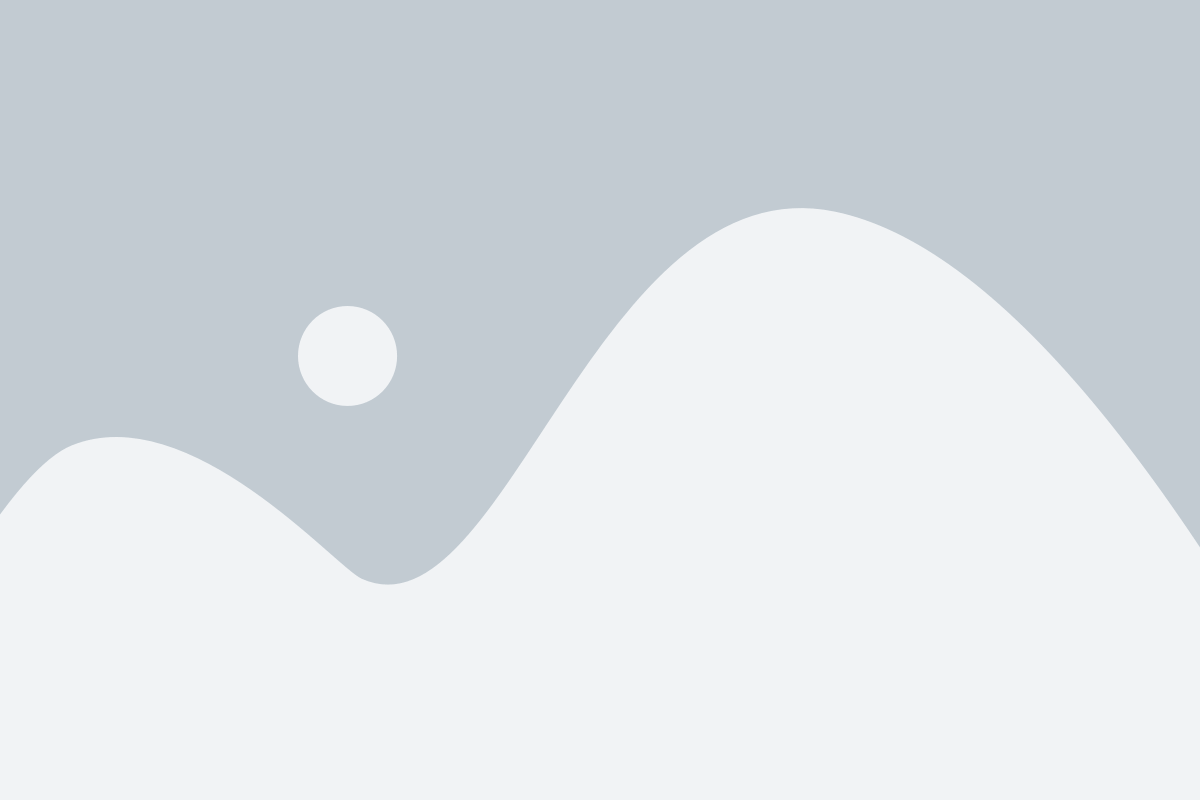
Carbon Fiber Quasi-3D Braided Textile Architecture Preform
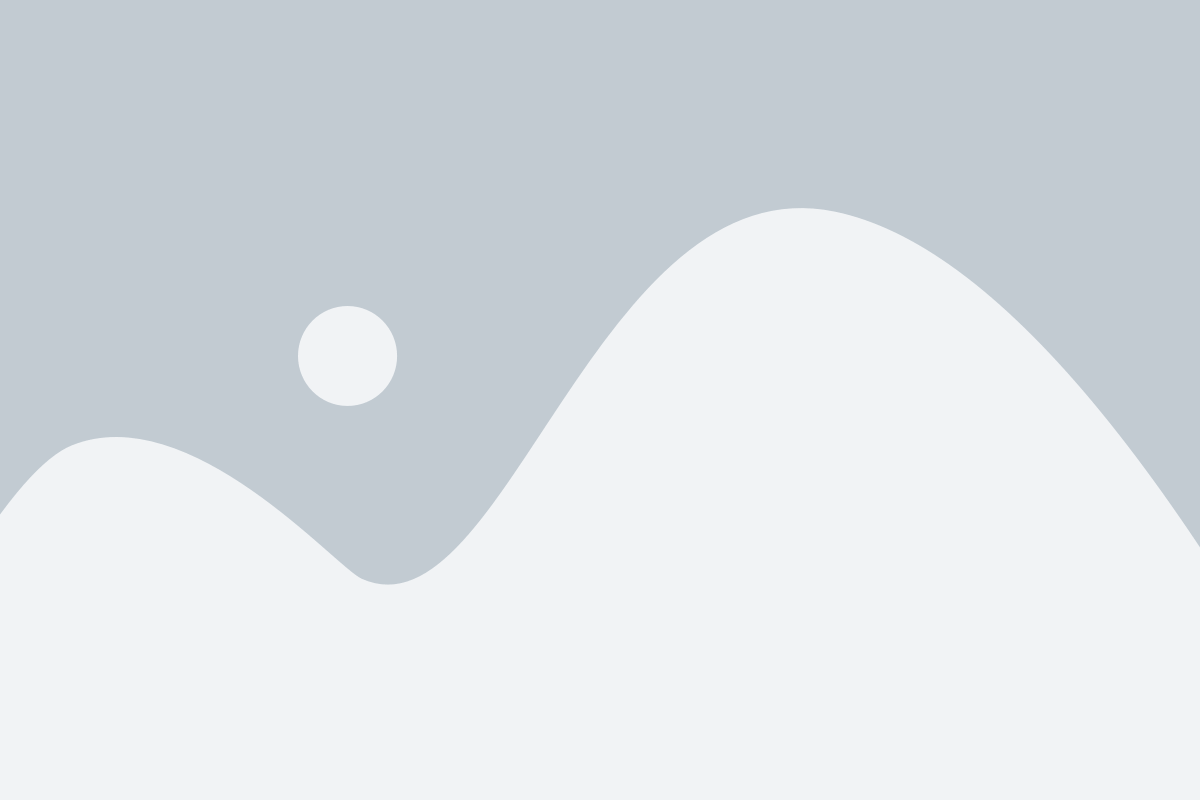
3D Braided Carbon Fiber Textile Architecture Preform
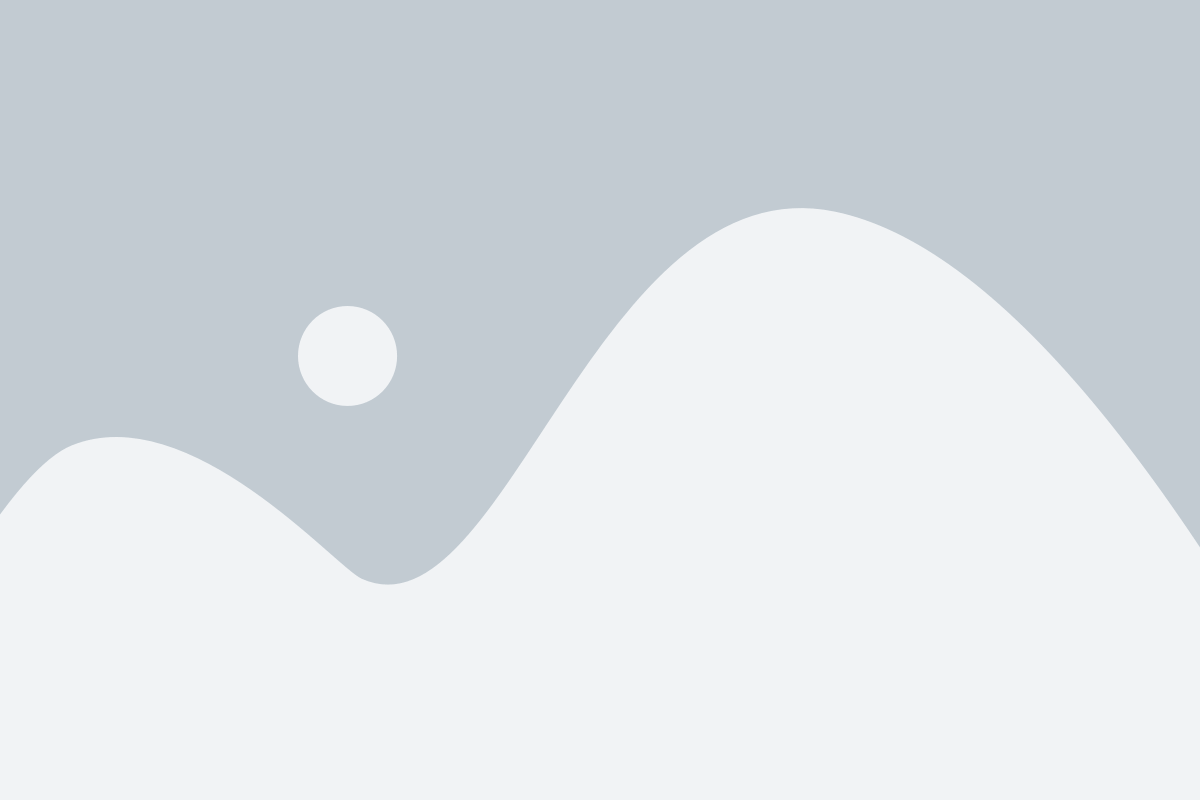
Hybrid 2.5D preform of quartz fiber/PAN-based carbon fiber or pitch-based carbon fiber/PAN-based carbon fiber
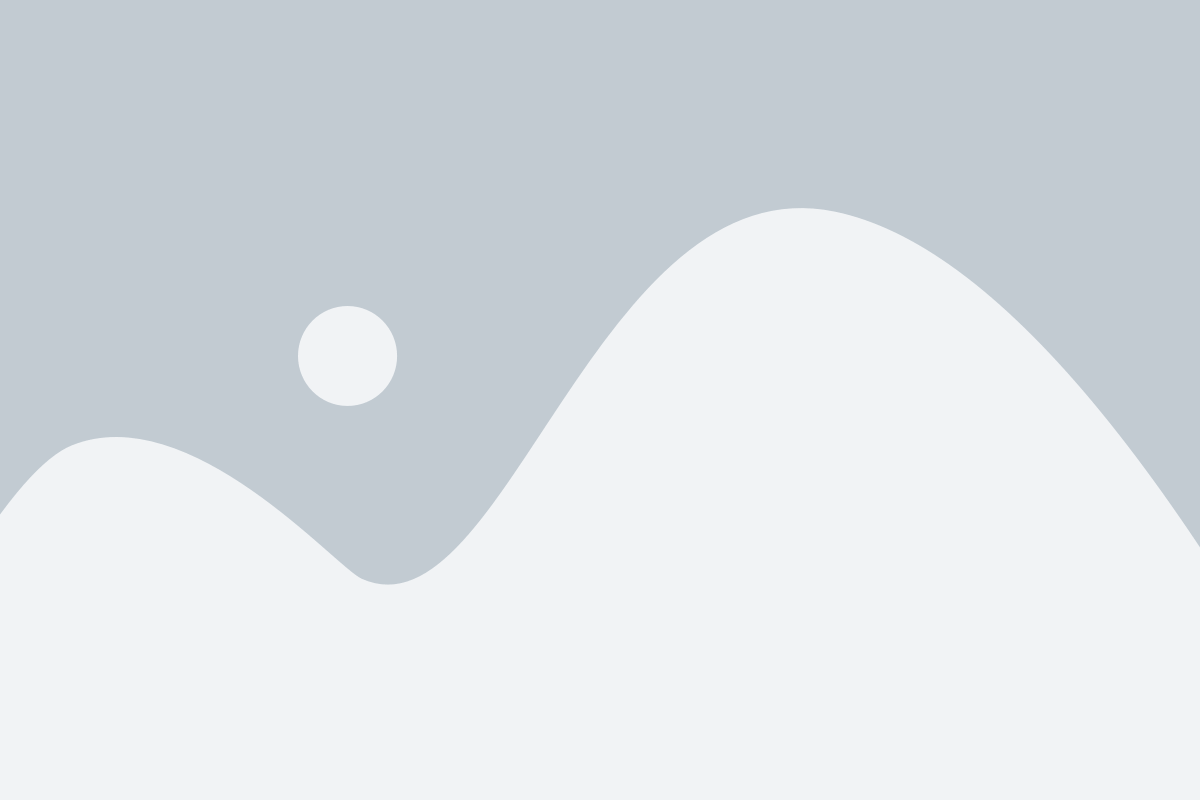
Pre-oxidized fiber or pre-oxidized fiber/PAN-based carbon fiber 2.5D preform
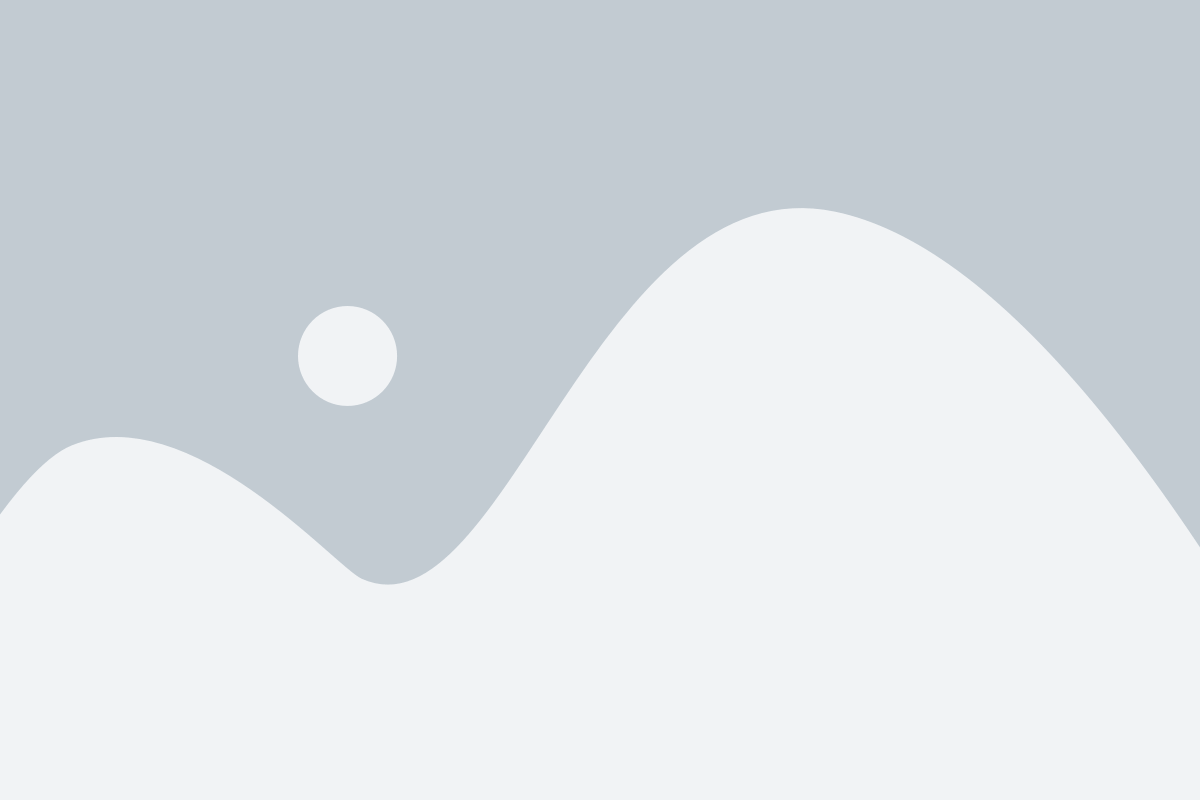
Hybrid 2.5D preform of quartz fiber/PAN-based
carbon fiber or pitch-based carbon fiber/PAN-based
carbon fiber
What is carbon fiber preforms used for?
Carbon fiber preforms are used as the foundational structure in the production of carbon fiber-reinforced composites, which are highly sought after in various high-performance applications due to their exceptional strength-to-weight ratio and stiffness. Here’s a breakdown of how carbon fiber preforms are utilized:
Composition and Manufacturing
Preforms are essentially ready-made pieces of carbon fiber fabric or mats, shaped to fit specific molds or parts. They are made by arranging carbon fiber in a desired three-dimensional shape or architecture, which is then impregnated with a resin matrix to form a composite material through processes like resin transfer molding or compression molding.
Key Uses of Carbon Fiber Preforms
Aerospace and Aviation:
- Structural Components: Used in the manufacture of critical load-bearing structures such as fuselage sections, wing assemblies, and tail components where high strength and low weight are essential.
- Interior Components: Used in seats, overhead compartments, and other cabin fixtures to reduce aircraft weight and enhance fuel efficiency.
Automotive Industry:
- Performance and Luxury Vehicles: Employed in the production of structural and aesthetic parts including chassis, body panels, and interior components for cars, particularly in high-performance and luxury vehicle segments.
- Electric Vehicles: Utilized to reduce the weight of the vehicle to offset the heavy batteries, thus improving range and performance.
Sports and Recreation:
- Equipment: Widely used in high-end sports equipment such as racing bicycles, golf clubs, tennis rackets, and poles for skiing and trekking, offering improved performance characteristics such as reduced weight and increased rigidity.
Marine:
- Boats and Yachts: Used in hulls, masts, and other components of boats and yachts where strength and resistance to the corrosive marine environment are required alongside significant weight savings.
Wind Energy:
- Turbine Blades: Integral in manufacturing large wind turbine blades that are both strong enough to withstand high winds and light enough to be efficient.
Construction and Infrastructure:
- Reinforcement: Applied in the construction of bridges, overpasses, and buildings, especially in earthquake-prone regions to provide additional strength without significant weight increase.
Benefits of Using Carbon Fiber Preforms
- Efficiency in Manufacturing: Preforms simplify the production process by allowing precise placement of fiber orientations and minimizing waste.
- Performance Enhancement: They ensure optimal alignment of fibers for load-bearing purposes, maximizing the mechanical properties of the final composite product.
- Weight Reduction: Significantly lighter than metals, contributing to enhanced performance in terms of speed, efficiency, and fuel consumption in vehicles and aircraft.
The versatility and superior properties of carbon fiber preforms make them indispensable in modern engineering and manufacturing, particularly where high strength, reduced weight, and durability are critical.